Achieve Weight Reduction and Precise Control with Core Back Foam Molding
ELK GROVE VILLAGE, IL, May 24, 2023 - Foam molding has emerged as a highly popular and versatile technique in the plastics industry. This method offers a plethora of advantages, ranging from significant part weight reduction and improved shock absorption to enhanced thermal insulation. By incorporating a foaming agent or gas into the resin during the molding process, foam molding enables the creation of lightweight, structurally sound components with unique properties.
However, achieving precise control over the foam state and ensuring consistent results has often posed challenges for manufacturers. That's where Shibaura Machine's Core Back Foam Molding steps in, improving the foam molding process by providing enhanced control and unprecedented accuracy.
Precision and Efficiency in Foam Molding
The Core Back Function offers unparalleled control over the foam molding process, enabling manufacturers to achieve precise control and consistent results. By adjusting the opening amount, speed, and time of the mold, manufacturers can ensure the creation of high-quality foam structures with the desired characteristics.
Part Weight Reduction
One of the standout advantages of the Core Back Function is its ability to achieve significant part weight reduction, particularly for large automotive parts. By carefully controlling the foaming process and integrating hollow sections within the molded parts, material consumption is reduced without compromising structural integrity. This weight reduction translates to cost savings, improved efficiency, and enhanced overall performance.
Enhanced Design Flexibility
Manufacturers can achieve design flexibility as this function enables the integration of complex internal features within molded parts, such as hollow sections and undercuts. Previously challenging or impossible to achieve, these intricate designs are now made possible, opening up new opportunities for innovative product designs.
Greater Control and Precision
The Core Back Function requires precision at a level of 0.01mm to maintain excellent foam quality through several advanced features:
- Clearance Counter System: By applying a preload between the movable platen and the link housing, the clearance on the link part is eliminated, ensuring precise control during the core back movement.
- Mold Opening Position Correction Control: Linear scales are added to maintain the actual position of the movable platen to match the set position, resulting in precise control over the foam molding process.
- Mold Platen Constant Speed Control: Varying the head speed of the mold opening process ensures consistent foam layer growth and bubble formation, leading to uniform foam distribution.
- Mold Opening Halt Circuit: This feature allows for setting precise halt positions and times during core back movement, facilitating adjustment of foam cell size and skin layer thickness.
Transform Your Foam Molding Process
With its ability to reduce part weight, enhance design flexibility, and provide precise control over foam molding processes, the Core Back Function opens up new opportunities for molders to produce lighter, more intricate, and functionally superior components.
Contact the Injection Molding Team to learn more about incorporating the Core Back Function into your process to achieve greater efficiency, cost savings, and improved product quality.
Tel: (888)593-1616
Email: im-success@shibaura-machine.com
Related Articles View All Articles
How Electric Ejectors Improve Injection Molding Performance
ELK GROVE VILLAGE, IL, November 16, 2022 - An electric ejector system can be a huge competitive differentiator compared to its hydraulic counterparts. The electric ejectors provide molders the ability to view torque giving better insight to allow for impro...
Read moreGive Your Injection Molding Parts Quality a Boost With Moldlyzer
ELK GROVE VILLAGE, IL, November 16, 2022 - The goal of any injection molding operation is 100% quality. Part of that process includes ensuring the injection pressure is right where it needs to be every time, in every stage of the operation. Without the rig...
Read moreExploring the Natural Pack Feature on the V70 Controller to Improve Injection Molding Processing
ELK GROVE VILLAGE, IL, November 9, 2022 - Manufacturers molding thin and/or long flow length parts are always looking for ways to reduce part defects. With high peak cavity pressure these applications can be particularly challenging. By being able to maxim...
Read moreBring Real-Time Quality Monitoring to the Injection Molding Floor with Shibaura Machine
ELK GROVE VILLAGE, IL, November 2, 2022 - How efficiently and effectively are you able to control your quality processes? When quality management is running smoothly it not only maintains quality but is focused on maximizing productivity creating the best ...
Read moreNow Enrolling for In-Person Injection Molding Training Courses
ELK GROVE VILLAGE, IL, August 3, 2022 - Shibaura Machine is pleased to announce our popular in-person injection molding training courses are resuming for the remainder of 2022. Customers can join us at our tech centers in Elk Grove Village, IL, Charlotte, ...
Read moreRobot Integration Simplified With Shibaura Machine
ELK GROVE VILLAGE, IL, June 29, 2022 - Automating tasks with robots has become an increasingly popular option for injection molding manufacturers. From placing inserts into molds to moving parts through post-mold processes, robots provide process stability...
Read moreWant to know more about our machines?
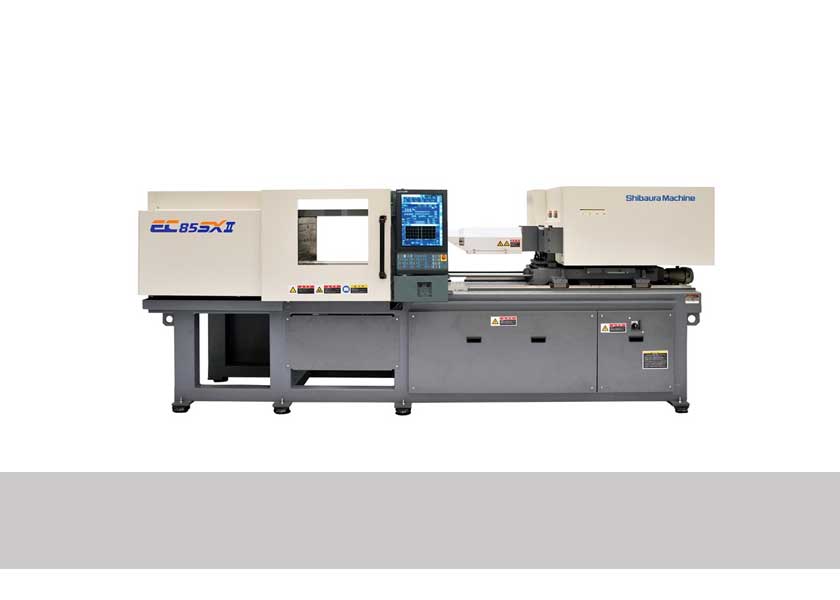
Injection Molding Machines
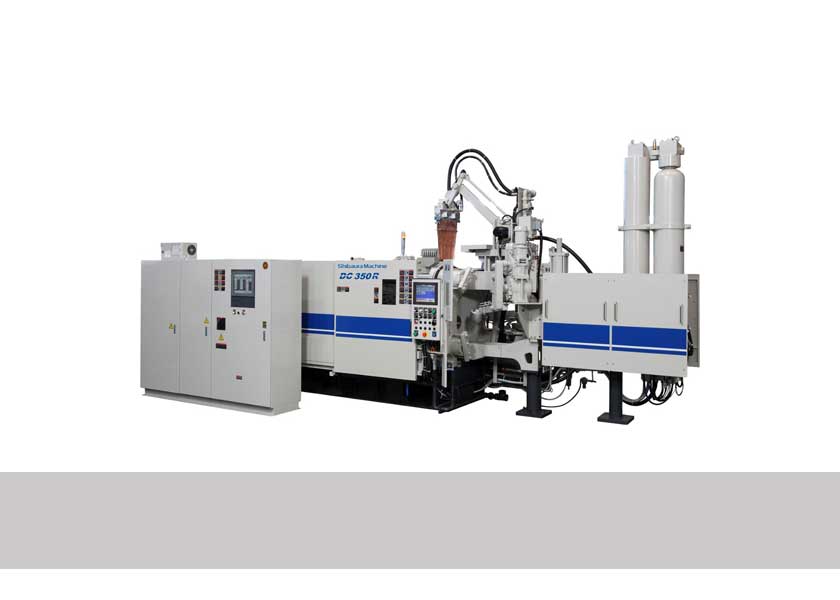
Die Casting Machines
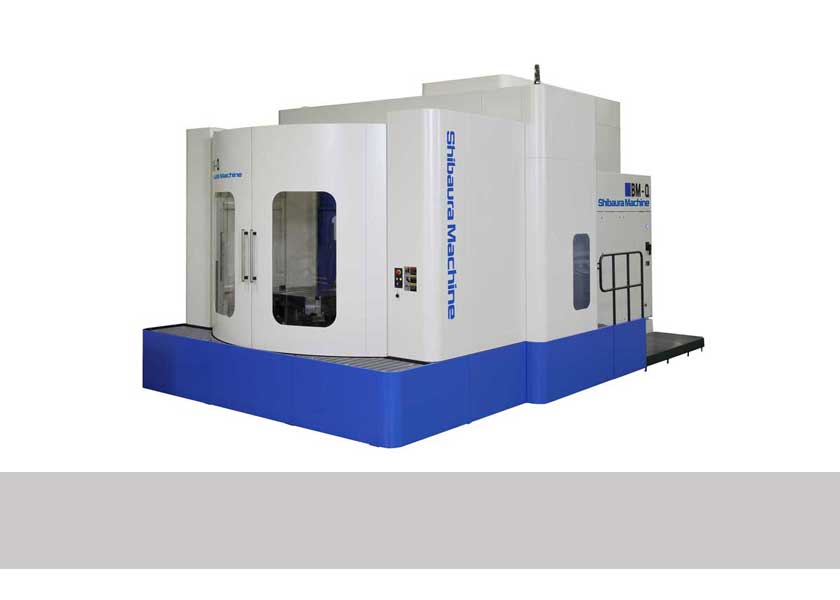
Machine Tools
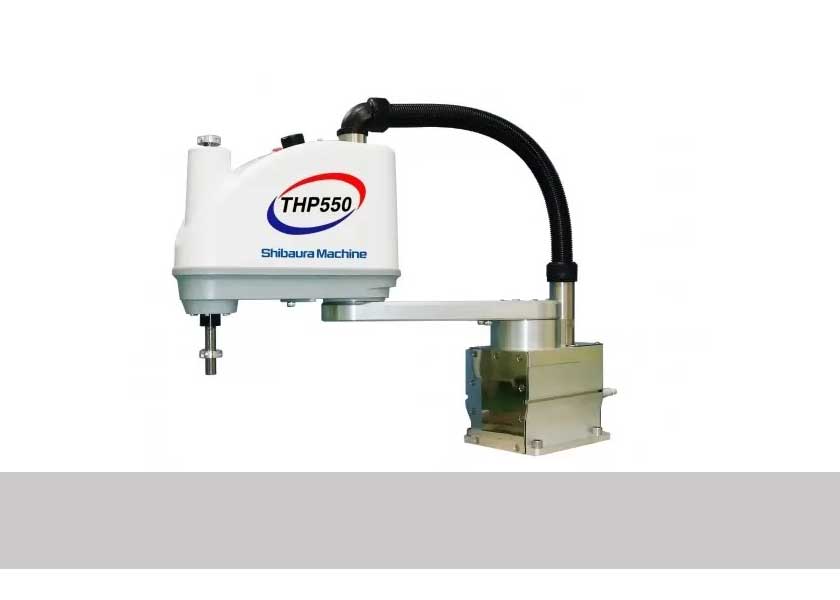