Maximizing Machine Tool Potential with High-Pressure Coolant Technology
ELK GROVE VILLAGE, IL, February 21, 2024 -
In the precision-driven world of machine tooling, the pursuit for efficiency, durability, and superior performance is constant. Among the multitude of technological advancements, the application of high-pressure coolant systems stands out as a game-changer in milling, turning, and drilling cutting tool performance.
For those looking to enhance their machining operations, understanding the specific advantages and applications of high-pressure coolant systems is the first step towards unlocking their full potential.
5 Ways Your Machine's Performance is Boosted with High-Pressure Coolant
1. Enhanced Chip Management
One of the primary advantages of high-pressure coolant systems is their ability to manage and remove chips effectively. Traditional low-pressure systems often struggle to clear chips from the cutting zone, leading to potential re-cutting that can damage the workpiece and diminish tool life.
High-pressure coolant forcefully evacuates chips from the cutting area, preventing them from interfering with the operation. This is particularly beneficial when machining materials that tend to produce long, stringy chips, which can wrap around the tool or workpiece, causing machine stoppages and additional wear on the tool.
2. Improved Tool Life
The intense localized pressure of coolant directly combats the heat caused at the cutting edge. By efficiently cooling the tool and workpiece, high-pressure systems minimize thermal deformation and wear, significantly extending tool life. This cooling effect also allows for higher cutting speeds and feeds, further optimizing production efficiency and reducing cost per part.
3. Increased Cutting Speeds and Productivity
High-pressure coolant systems enable machine tools to operate at higher speeds without compromising tool integrity or part quality. For example, in drilling the direct application of coolant at the cutting zone not only dissipates heat more effectively but also lubricates the cutting edge, reducing friction and allowing for smoother, faster cuts. This results in a noticeable boost in productivity, as operations can be completed more quickly without sacrificing precision or surface finish.
4. Enhanced Surface Finish and Tolerances
The precision of the final workpiece is crucial in manufacturing. High-pressure coolant contributes to superior surface finishes by ensuring consistent temperature control and removing chips efficiently, which might otherwise mar the surface of the part. The stability provided by the coolant pressure also aids in maintaining tight tolerances, essential for high-precision components in industries such as aerospace, automotive, energy, and medical devices.
5. Versatility Across Materials
High-pressure coolant systems are not limited to specific materials; they offer considerable advantages across a wide range of workpiece materials, from soft aluminum to hard-to-machine alloys like titanium and Inconel. The adaptability of high-pressure coolant makes it an invaluable tool in shops that deal with diverse machining tasks such as turning, milling, and drilling providing optimal conditions for each material's unique properties.
Elevate Your Manufacturing with Shibaura Machine
As industries continue to push the boundaries of machining efficiency and precision, the role of high-pressure coolant in achieving these goals becomes increasingly indispensable. Shibaura Machine, with its commitment to innovation and excellence, provides advanced machine tools that can be equipped with optional high-pressure coolant systems, designed to meet the demanding needs of modern manufacturing.
Contact Shibaura Machine's Machine Tools team to explore how high-pressure coolant can revolutionize your cutting performance and help your business thrive in the competitive landscape of manufacturing.
Related Articles View All Machine Tools Articles
Engineering Excellence: A Closer Look at Shibaura Machine's TUE Series Tool Holders
ELK GROVE VILLAGE, IL, February 6, 2024 - Shibaura Machine's TUE series machines are equipped with a diverse range of tool holders, each designed to maximize functionality and versatility. These tool holders are integral to the TUE series catering to a wid...
Read moreThe Future of Machine Tool Support: Introducing Shibaura Machine's Customer Portal
ELK GROVE VILLAGE, IL, January 30, 2024 - As we get ready to launch our new Customer Service Portal for Machine Tool customers later this year, Shibaura Machine Company, America is leading the way in transforming how you access information and receive supp...
Read moreElevating Customer Support in Machine Tools: Shibaura Machine's Integration of CRM and Smart Glasses
ELK GROVE VILLAGE, IL, January 23, 2024 - In an era where digital transformation is not just a trend but a business imperative, Shibaura Machine Company, America continues to grow our virtual customer support options in the machine tool industry. Building ...
Read moreTransforming Machine Tool Maintenance: Shibaura Machine’s Remote Assist Service
ELK GROVE VILLAGE, IL, January 9, 2024 - In the face of rapidly advancing technology and ever-increasing global competition, the manufacturing industry stands at a pivotal crossroads. Shibaura Machine understands the critical need for speed, efficiency, an...
Read moreExploring the TOSNUC PX200 CNC Control: A Smart Machining Partner
ELK GROVE VILLAGE, IL, December 13, 2023 - Today's manufacturing world moves fast, and being precise, efficient, and easy to use is more important than ever. This week we're highlighting TOSNUC PX200 Controller, which is more than just a CNC control syste...
Read moreInnovation and Precision at the Center the FANUC 31i-B Plus CNC Control
ELK GROVE VILLAGE, IL, December 5, 2023 - The FANUC 31i-B Plus marks a significant advancement in machine tool CNC control technology. Known for its efficiency and exceptional features, it's designed for modern, complex machines, driving innovation in mach...
Read moreWant to know more about our machines?
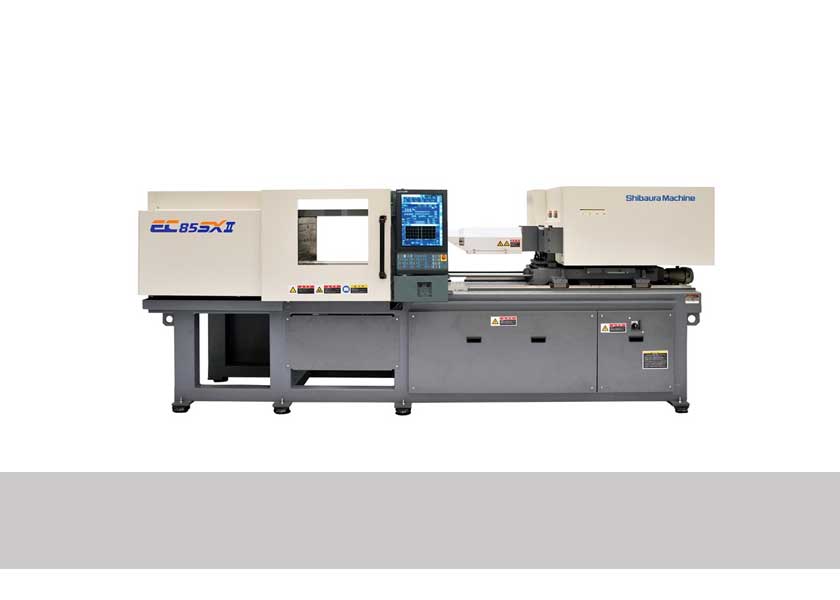
Injection Molding Machines
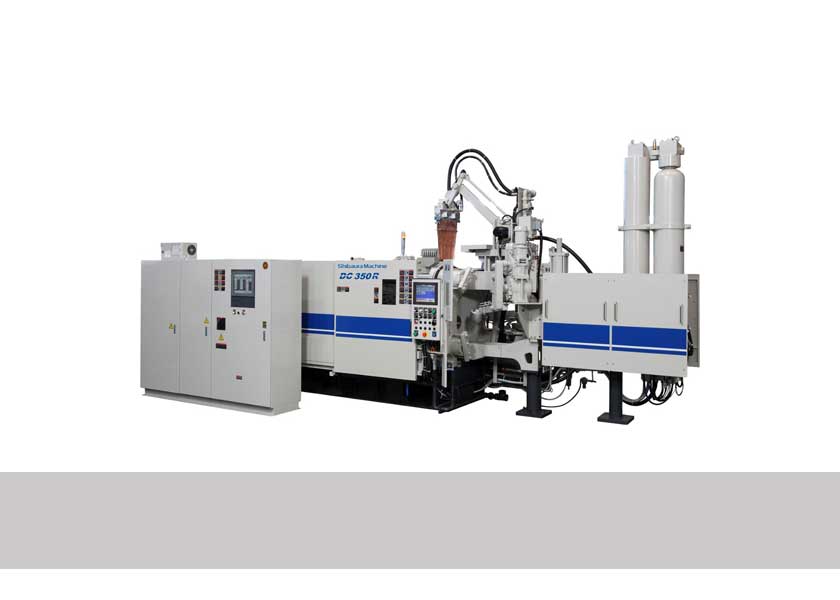
Die Casting Machines
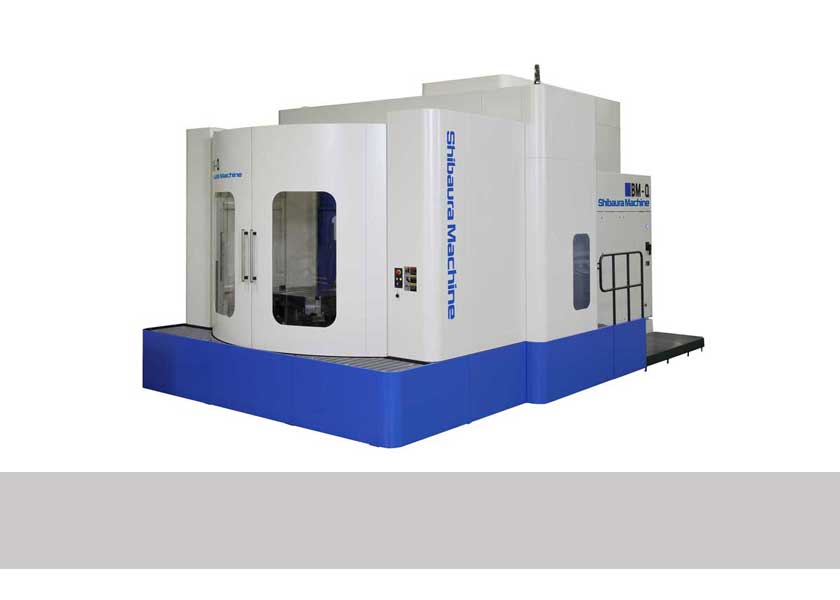
Machine Tools
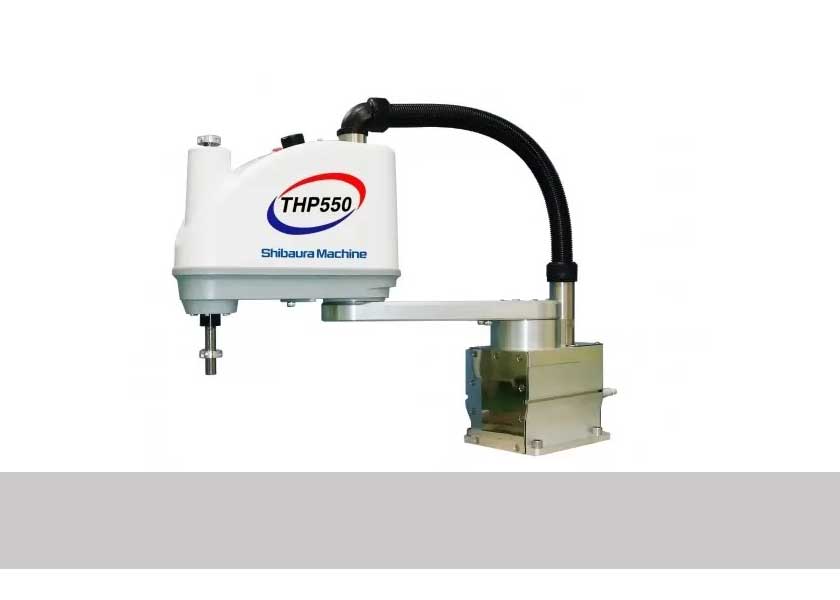