Reduce Cooling Water Load with All-Electric Machines
ELK GROVE VILLAGE, IL, February 2, 2022 - Water cooling systems have long been used in hydraulic injection molding machines in order to keep the machine running smoothly. But imagine being able to reduce cooling water load requirements- it will allow you to not only reduce production costs and increase efficiency. Thanks to all-electric injection molding machines, manufacturers no longer need to utilize large water cooling systems to keep their machine running, allowing them to reduce overall cooling water load while improving energy efficiency.
Less Water, More Benefits
The SXIII all-electric injection molding machine allows manufacturers to optimize their cooling demands and reduce energy usage.
All-electric machines eliminate the need for cooling water with the exception of one circuit. The only cooling water needed is supplied to the feed throat, which is controlled with a solenoid valve. This ensures efficient control of the flow and temperature of the feed throat area.
Running on servo motors, it not only reduces the cooling water needed, but also the associated increased energy use that goes along with hydraulic systems. Fans are used to cool the electric cabinets and the servo motors are air cooled and sized properly. In addition, all-electric machines require no hydraulic oil which not only saves on water cooling of the hydraulic oil, but also means no heat exchangers are needed.
Start Saving
Reducing your cooling water load with an all-electric machine will not only save on production costs, but help your factory towards reducing energy usage and your overall carbon footprint. Contact the Injection Molding Team to learn more about the SXIII series.
Tel: (888) 593-1616
Contact us today to discuss how our all-electric technology can help you reduce costs!
Related Articles View All Articles
Why Repeatability and All-Electric Molding Machines Go Hand in Hand
ELK GROVE VILLAGE, IL, January 23, 2022 - Repeatability in injection molding. Being able to offer this shot after shot means lower cost of operation and consistency. It is key to the production of parts in today’s competitive market and has a crucial influ...
Read moreLooking to Reduce Scrap? Why All-Electric Injection Molding Machines Are the Clear Choice
ELK GROVE VILLAGE, IL, January 12, 2022 - Improving scrap rates in injection molding can have a large impact on increasing profitability. While there are many process improvements for scrap rate reduction, it is also important to consider the type of machi...
Read moreFaster Cycle Times with All-Electric Injection Molding
ELK GROVE VILLAGE, IL, January 6, 2022 - Considering changing out from hydraulic to all-electric machines in the new year, but trying to justify the change? Look no further than the improvements these machines can make to your cycle time. Being able to red...
Read moreHow Automatic Load Cell Calibration Helps Prevent Molding Defects
ELK GROVE VILLAGE, IL, December 29, 2021 - One of the key advantages of all-electric injection molding machines is the ability to monitor actual plastic pressure during injection via a load cell behind the screw, without the need for in-mold transducers. ...
Read moreHow the I/O Checker Minimizes Machine Downtime for Injection Molders
ELK GROVE VILLAGE, IL, December 21, 2021 - Creating injection molded parts not only requires a high level of technical expertise, but also attention to detail. One small mistake can slow down, or even stop production.How many times this year have machine d...
Read moreHow the Mold Guide Makes Set-Up Simple and Efficient
ELK GROVE VILLAGE, IL, December 16, 2021 - Installing a mold in an injection molding machine is a routine process. However, even when tasks are routine, mistakes can be made. Being able to perfect mold change-overs and lessen mistakes can not only help imp...
Read moreWant to know more about our machines?
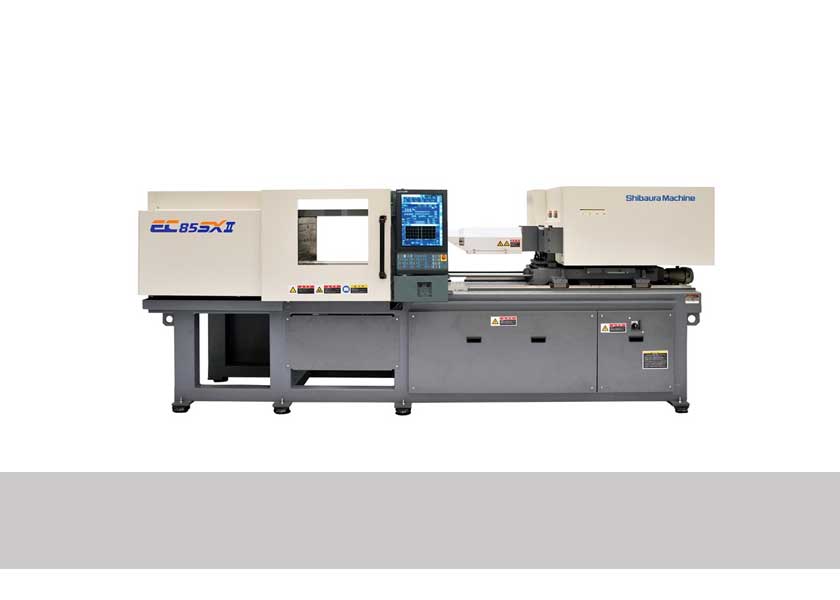
Injection Molding Machines
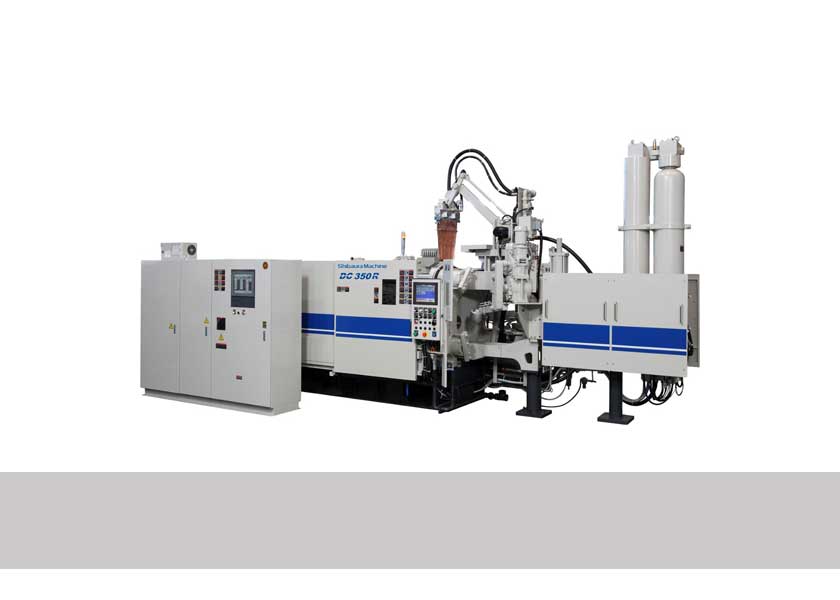
Die Casting Machines
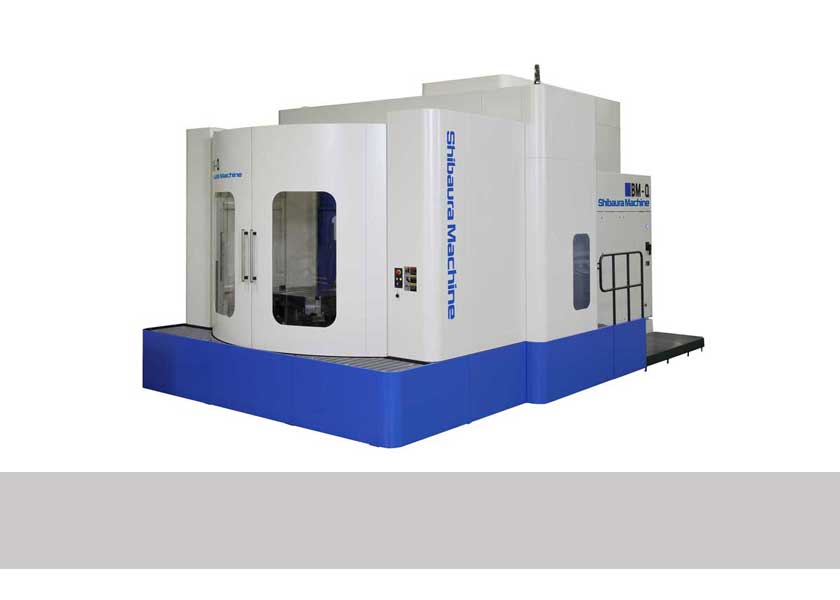
Machine Tools
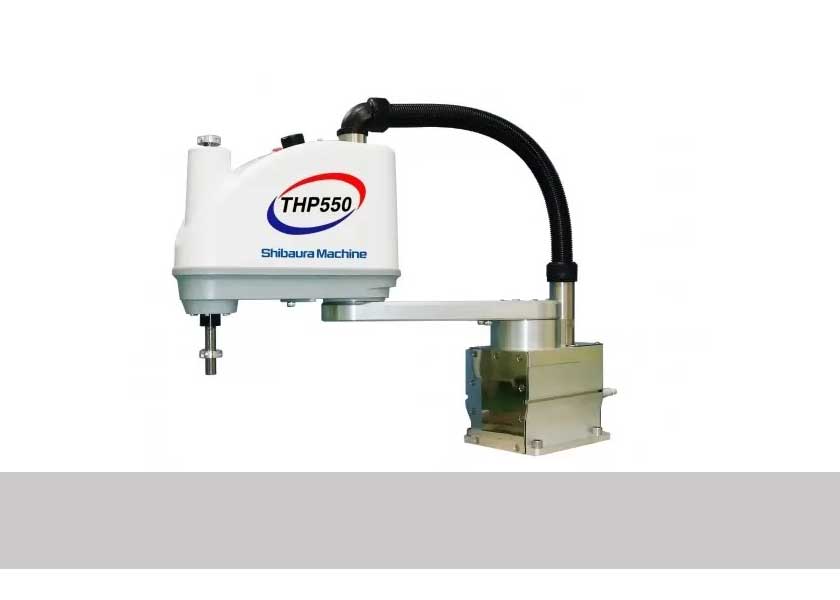