What to Consider When Looking at Full Enclosures for Your Horizontal Boring Machine
ELK GROVE VILLAGE, IL, March 5, 2024 -
The adoption of horizontal boring machines equipped with full enclosures marks a significant stride in manufacturing towards operational excellence and safety. As businesses strive to enhance their manufacturing capabilities, understanding the multifaceted considerations associated with integrating these advanced machines into existing operations becomes paramount.
This article aims to shed light on the critical aspects of incorporating horizontal boring machines with full enclosures, from spatial requirements and system compatibility to ensuring operational efficiency and upholding stringent safety standards.
What to Consider with Horizontal Boring Machines and Full Enclosures
When integrating horizontal boring machines (HBMs) equipped with full enclosures into your manufacturing operations, several key considerations can help ensure you maximize the benefits while addressing potential challenges.
Compatibility and Integration
- Space Requirements: It's essential to assess your facility's available space to accommodate the enclosure without compromising operational efficiency.
- Integration with Existing Systems: Consider how a fully enclosed machine will integrate with your current workflow and systems. For example, material handling, chip disposal, and coolant management systems may need adjustments to work seamlessly with an enclosed setup.
Operational Efficiency
- Access for Maintenance and Setup: Full enclosures may make access for maintenance, setup, and tool changes more challenging. Look for enclosure designs that offer easy access panels or doors that facilitate routine tasks.
- Visibility: Ensure that the enclosure design provides adequate visibility for operators to monitor the machining process. This may include large windows, adequate lighting, and possibly camera systems for real-time monitoring.
Safety Features
- Interlock Systems: Safety interlocks prevent the machine from operating when the enclosure is open. Verify that the machine's safety features comply with relevant standards and regulations to protect operators.
- Emergency Stops: Accessibility to emergency stop buttons from outside the enclosure is crucial. Placement should be strategic to allow quick responses in case of an emergency.
Environmental Control
- Coolant and Chip Management: Enclosures can help contain chips and coolant spray, but effective management systems are necessary to remove chips and maintain a clean environment inside the enclosure.
- Ventilation and Air Quality: Consider the need for ventilation systems to manage air quality, especially if the machining process generates significant coolant mist.
Operator Preparation
- Training: Ensure that operators are adequately trained to work with fully enclosed machines. This includes understanding safety features, maintenance procedures, and how to effectively monitor and adjust machining processes.
- Adaptation Period: Allow for a transition period where operators and maintenance personnel can become familiar with the new equipment. This period is crucial for identifying and resolving any operational challenges that may arise.
Modern Manufacturing
As full enclosures becomes increasingly essential in maintaining a clean and safe work environment, choosing the right one becomes crucial. Our Machine Tools Team guides manufacturers through the enclosure selection process to make sure they select the right enclosure for their applications.
With a commitment to innovation and excellence, Shibaura Machine is dedicated to helping manufacturers navigate the evolving world of machining, making the journey towards adopting full enclosures as seamless and beneficial as possible.
Related Articles View All Machine Tools Articles
Understanding Chip Management: Selecting the Correct Type of Chip Conveyor for Your Machining Needs
ELK GROVE VILLAGE, IL, February 27, 2024 - In the machining industry, precision and efficiency are key. Chip conveyors play an essential role in this environment, quietly ensuring machine tools stay clean and operational. Choosing the right size of chip co...
Read moreMaximizing Machine Tool Potential with High-Pressure Coolant Technology
ELK GROVE VILLAGE, IL, February 21, 2024 - In the precision-driven world of machine tooling, the pursuit for efficiency, durability, and superior performance is constant. Among the multitude of technological advancements, the application of high-pressure c...
Read moreEngineering Excellence: A Closer Look at Shibaura Machine's TUE Series Tool Holders
ELK GROVE VILLAGE, IL, February 6, 2024 - Shibaura Machine's TUE series machines are equipped with a diverse range of tool holders, each designed to maximize functionality and versatility. These tool holders are integral to the TUE series catering to a wid...
Read moreThe Future of Machine Tool Support: Introducing Shibaura Machine's Customer Portal
ELK GROVE VILLAGE, IL, January 30, 2024 - As we get ready to launch our new Customer Service Portal for Machine Tool customers later this year, Shibaura Machine Company, America is leading the way in transforming how you access information and receive supp...
Read moreElevating Customer Support in Machine Tools: Shibaura Machine's Integration of CRM and Smart Glasses
ELK GROVE VILLAGE, IL, January 23, 2024 - In an era where digital transformation is not just a trend but a business imperative, Shibaura Machine Company, America continues to grow our virtual customer support options in the machine tool industry. Building ...
Read moreTransforming Machine Tool Maintenance: Shibaura Machine’s Remote Assist Service
ELK GROVE VILLAGE, IL, January 9, 2024 - In the face of rapidly advancing technology and ever-increasing global competition, the manufacturing industry stands at a pivotal crossroads. Shibaura Machine understands the critical need for speed, efficiency, an...
Read moreWant to know more about our machines?
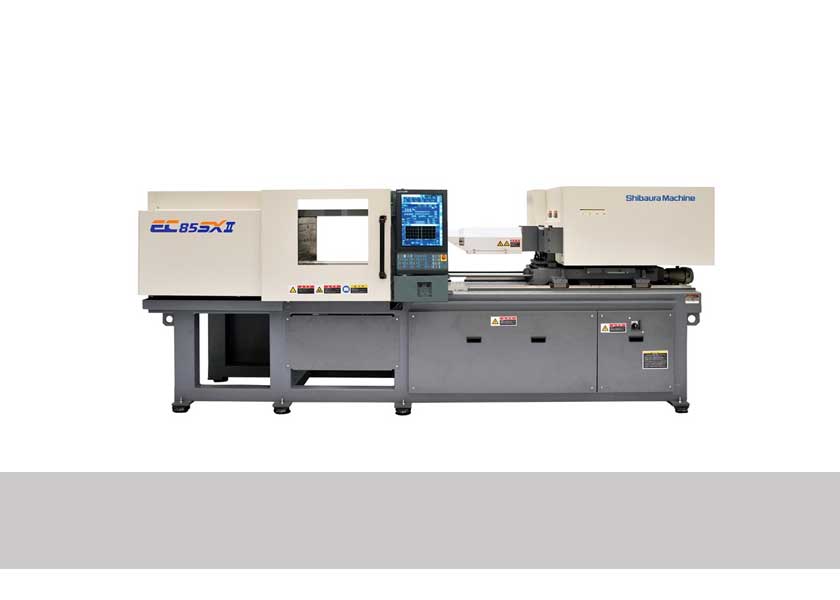
Injection Molding Machines
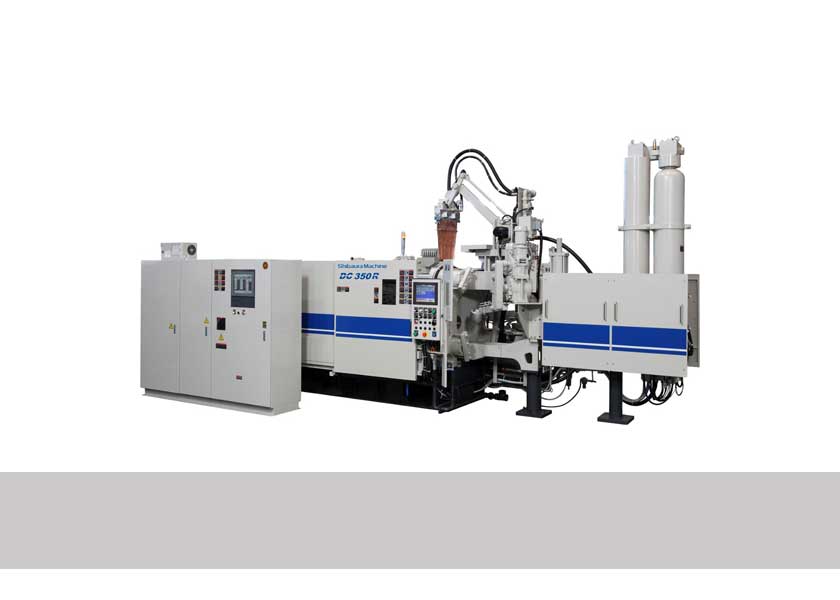
Die Casting Machines
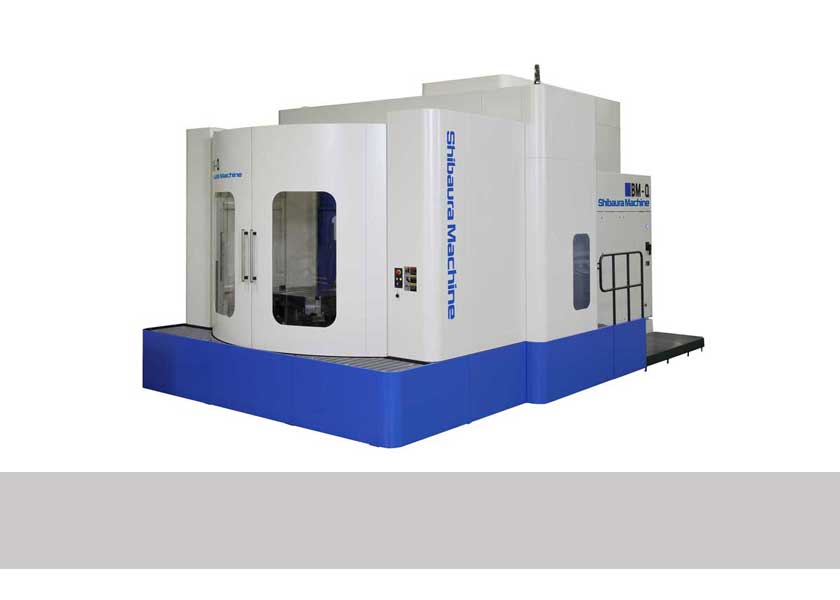
Machine Tools
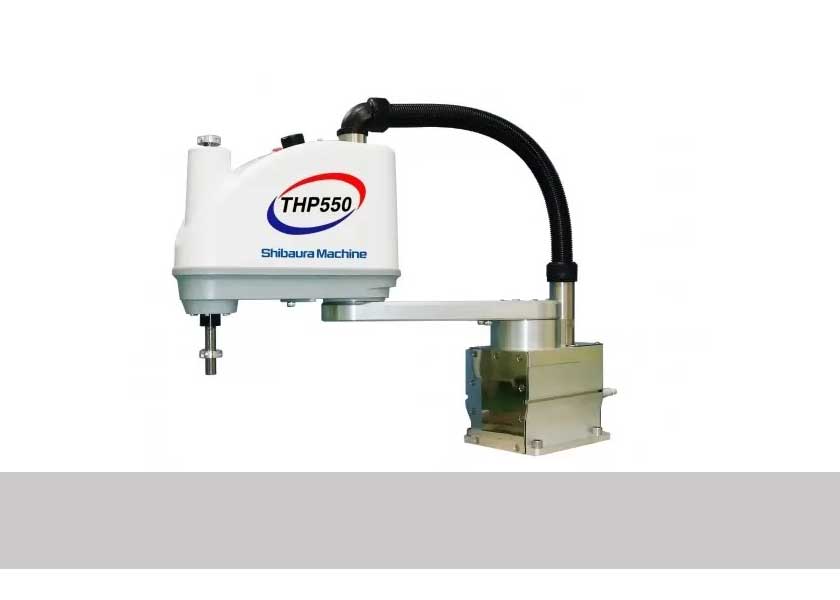