Mastering Material Changeovers in Injection Molding
ELK GROVE VILLAGE, IL, August 8, 2023 - Optimizing efficiency and minimizing costs are crucial to success in the fast-paced world of injection molding. However, one aspect that often poses difficulties for molders is the purging process.
The traditional method of purging has been commonly associated with wasting time, materials, and hindering productivity. It has been challenging finding an effective way to automate the process of switching between different materials or colors.
Common Challenges with Traditional Purging Methods
Downtime and Lost Production
Conventional purging methods require machine stoppage, cleaning, and setup changes. For instance, manual purging requires intensive labor, can be difficult to monitor, and has been known to cause inconsistent quality. This results in significant downtime, leading to lost production time and decreased efficiency.
Material Waste and Scrap Parts
Improper purging can leave behind residual materials in the barrel, causing contamination and affecting the quality of subsequent production runs. For example, when switching from a black material to a white material, residue left behind in the barrel can cause a gray-colored part to be produced. This leads to increased scrap parts and wasted materials, impacting profitability.
Maintenance and Tooling Issues
Carbon build-up in the barrel and color hang-ups in the tool can lead to frequent maintenance requirements and decreased tool life. These challenges further contribute to increased downtime and maintenance costs.
Screw and Barrel Damage
Traditional purging methods in injection molding can lead to damage of the screw and barrel due to excessive screw RPM’s and other factors. Purging with the same resin at elevated temperatures can cause localized overheating, resulting in thermal degradation and residue buildup. Moreover, conventional purging compounds can wear down these components, leading to increased clearances and diminished performance. Excessive compression forces during traditional purging can further contribute to fatigue on the screw and barrel. Additionally, such methods may not adequately clean hard-to-reach areas, leaving behind traces of old material or contaminants.
Finding a Solution with Auto Purge
Automated purging systems are known to reduce the amount of time and materials needed to purge a machine. Additionally, automating a purge can save an extensive amount of purge material that would otherwise be wasted. Shibaura Machine's V70 controller is equipped with the innovative Auto Purge feature, which provides an integrated comprehensive solution to address these pain points.
Seamless Transition and Reduced Downtime
By automating the purging process, it eliminates downtime associated with manual cleaning, reducing production interruptions, and increasing overall equipment efficiency. For instance, a user can pre-program a purge sequence so they no longer need to manually make changes to the process.
Improved Material Purging
The Auto Purge feature ensures thorough purging of residual materials from the barrel, preventing contamination and maintaining product quality. It offers multiple operation modes, including program purge, screw speed purge, and customized purge, tailored to specific materials and production requirements.
For example, the program purge mode allows for a customizable sequence of purging operations, including RPMs, back pressure, and stroke to optimize the purging process with no manual intervention.
Extended Maintenance Intervals
Thorough purging facilitated by the Auto Purge feature ensures that each production run starts with a clean and uncontaminated barrel. By minimizing carbon build-up in the barrel and eliminating color hang-ups in the tool, the Auto Purge feature helps extend the time between required maintenance intervals for molds and enhances operational efficiency. This process minimizes the risk of rejects or customer complaints, resulting in consistent product quality.
Reduce Operator Error
With a one-touch, pre-programmed auto-purge program, it replaces manual setup of speeds, positions, and pressures, reducing human error. This automated process ensures consistency and accuracy even with operator shift changes throughout the day. By preventing improper color changes and reducing scrap, auto purging minimizes the risk of mistakes that could lead to costly production issues.
For instance, an operator setting a screw RPM too high during manual purging might cause damage to the screw, screw tip assembly and barrel and could cause resin degradation, especially with materials like PVC. With automated purging, such risks are mitigated, leading to improved efficiency, reduced downtime, and enhanced product quality.
Simplify Purging and Boost Productivity
Shibaura Machine's Auto Purge feature on the V70 controller improves the injection molding process by addressing the challenges and pain points associated with conventional purging. By automating the process through its intuitive interface, manufacturers can significantly reduce downtime, material waste, and maintenance requirements.
To realize the full potential of your injection molding process and leverage the Auto Purge feature, reach out to our Injection Molding team.
Tel: (888) 593-1616
Email: im-success@shibaura-machine.com
Related Articles View All Articles
Partnering for Success: Shibaura Machine's Technical Sales Support Services
ELK GROVE VILLAGE, IL, July 20, 2023 - As the manufacturing landscape continues to evolve, having a reliable technical sales support team becomes increasingly important. With inefficiencies in injection molding processes translating into financial losses, ...
Read moreInvest in Your Success: Shibaura Machine's Training Programs for Injection Molding Professionals
ELK GROVE VILLAGE, IL, July 5, 2023 - When it comes to injection molding, having a well-trained team is crucial for maximizing machine performance and achieving optimal results. Training ensures that all personnel understand not only the machine's capabili...
Read moreAchieving Injection Molding Excellence with Integrated Auxiliary Equipment
ELK GROVE VILLAGE, IL, June 21, 2023 - Staying ahead of the competition in manufacturing requires adopting innovative solutions that enhance productivity and efficiency. Auxiliary equipment offers a way to enable precise and automated handling of materials...
Read moreDriving Sustainable Development: The Rise of All-Electric Injection Molding Machines
ELK GROVE VILLAGE, IL, June 7, 2023 - As sustainability becomes an increasingly important focus worldwide, industries are seeking innovative solutions to align their operations with the United Nations' Sustainable Development Goals (SDGs). In the world of ...
Read moreAchieve Weight Reduction and Precise Control with Core Back Foam Molding
ELK GROVE VILLAGE, IL, May 24, 2023 - Foam molding has emerged as a highly popular and versatile technique in the plastics industry. This method offers a plethora of advantages, ranging from significant part weight reduction and improved shock absorption t...
Read morePrecision Optics and Thin-Wall Molding Made Easier with PRESTROL
ELK GROVE VILLAGE, IL, May 10, 2023 - In order to produce high-quality parts with consistent properties and dimensions, it's important to achieve uniform distribution of material within the mold cavity during the injection process. However, this continues ...
Read moreWant to know more about our machines?
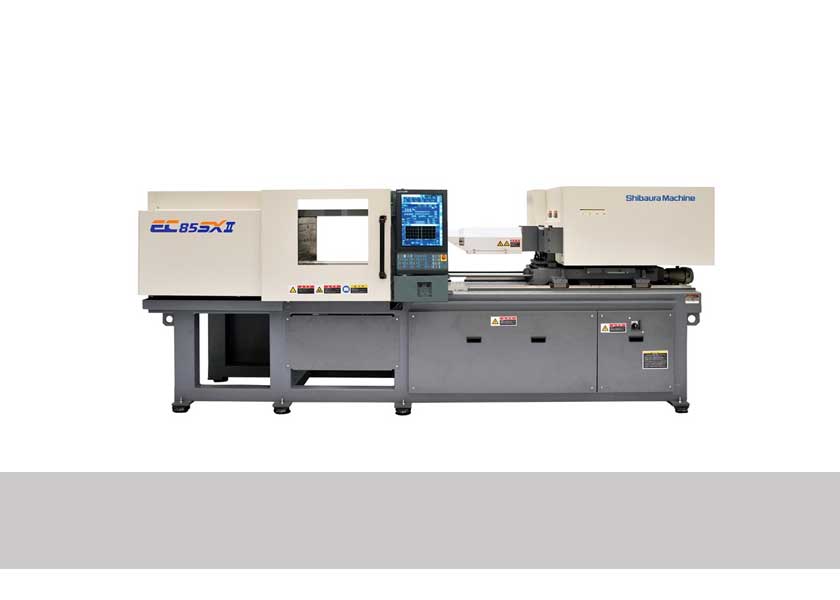
Injection Molding Machines
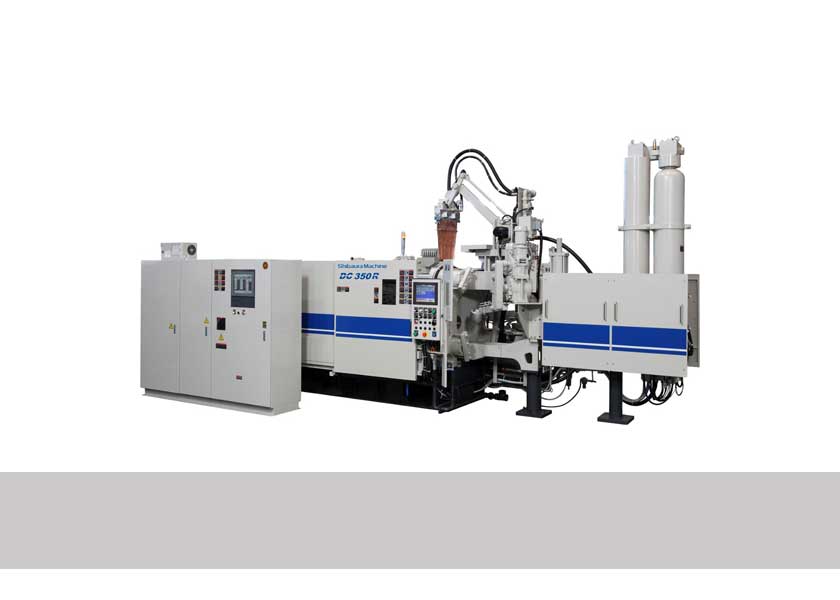
Die Casting Machines
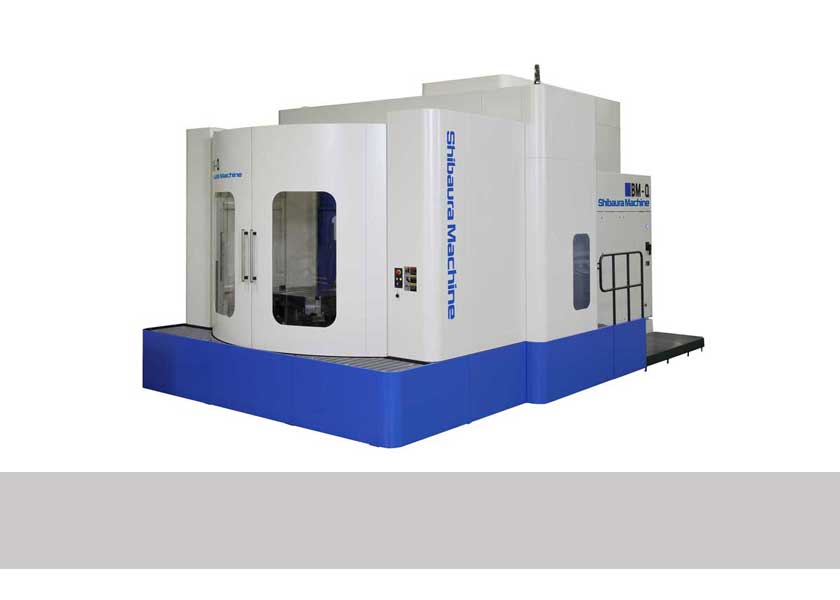
Machine Tools
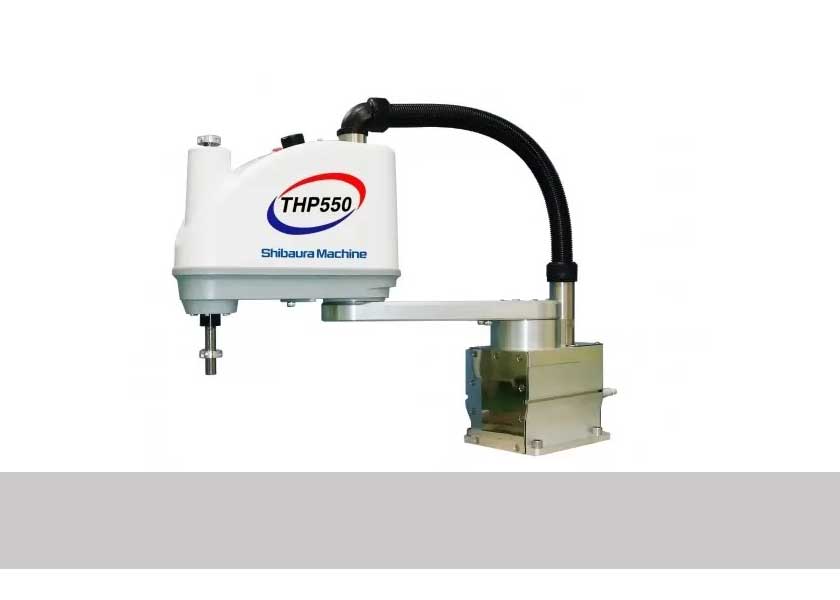