Give Your Injection Molding Parts Quality a Boost With Moldlyzer
ELK GROVE VILLAGE, IL, November 16, 2022 - The goal of any injection molding operation is 100% quality. Part of that process includes ensuring the injection pressure is right where it needs to be every time, in every stage of the operation. Without the right technology in place, it can be hard for the process technician to ensure proper pressure control.
The V70 controller’s Moldlyzer function provides an ideal solution for the process technician providing the data they need to make sure each shot is within proper ranges. This easy-to-use injection pressure monitoring tool provides metrics on the injection process from start to finish and comparative analysis against past shots.
Tailored Pressure Monitoring Improves Quality
Instead of monitoring the whole injection process, this function breaks injection into four zones for more accurate data: start, middle, pack, and hold. This quality monitoring function takes it a step further once the process is stable, by recording multipoint sampling of the injection pressure curve. The results of when a good quality part is produced is then used as a reference point. Using this reference point it automatically compares subsequent shots against the reference sample.
Within the four zones, there are 3 different monitoring methods that can be used to further understand quality.
- Area method compares the average pressure deviation and tolerance. This data can confirm molding stability at initial auto operation after approximate set-up data has been filtered down. This is the standard method of quality monitoring.
- Multi-point method compares the pressure deviation and tolerance per sampling. This method can be used to investigate parts where pressure change is unstable.
- Single-point method only monitors a single specific point and is used when pressure variations in a certain point greatly affect product quality.
For all four zones, the option to set the PMAX Alarm is available. This alarm can be used to prevent overpacking causing the injection operation to stop immediately when the detection pressure setting is exceeded.
Start Improving Shot Quality Today
Achieving zero-defect production requires reliable process control and can prove difficult without the right technology in place. Shibaura Machine’s V70 controller provides a solution for process technicians with a variety of easy-to-use quality monitoring tools to measure and analyze the injection molding process from start to finish. Learn more about the Moldlyzer function and all the process control features on the V70 controller by contacting the Injection Molding team today.
Tel: (888)593-1616
Email: im-success@shibaura-machine.com
Related Articles View All Articles
Exploring the Natural Pack Feature on the V70 Controller to Improve Injection Molding Processing
ELK GROVE VILLAGE, IL, November 9, 2022 - Manufacturers molding thin and/or long flow length parts are always looking for ways to reduce part defects. With high peak cavity pressure these applications can be particularly challenging. By being able to maxim...
Read moreBring Real-Time Quality Monitoring to the Injection Molding Floor with Shibaura Machine
ELK GROVE VILLAGE, IL, November 2, 2022 - How efficiently and effectively are you able to control your quality processes? When quality management is running smoothly it not only maintains quality but is focused on maximizing productivity creating the best ...
Read moreNow Enrolling for In-Person Injection Molding Training Courses
ELK GROVE VILLAGE, IL, August 3, 2022 - Shibaura Machine is pleased to announce our popular in-person injection molding training courses are resuming for the remainder of 2022. Customers can join us at our tech centers in Elk Grove Village, IL, Charlotte, ...
Read moreRobot Integration Simplified With Shibaura Machine
ELK GROVE VILLAGE, IL, June 29, 2022 - Automating tasks with robots has become an increasingly popular option for injection molding manufacturers. From placing inserts into molds to moving parts through post-mold processes, robots provide process stability...
Read moremachiNetCloud Industrial IoT Now Included on New Injection Molding Machines
ELK GROVE VILLAGE, IL, June 22, 2022 - As the landscape in manufacturing continues to rapidly change due to digitalization, the Industrial Internet of Things (IIoT) brings a great opportunity to gain a competitive advantage in every form of production, inc...
Read moreCustomize Your Clamping Sequence at a Touch
ELK GROVE VILLAGE, IL, June 17, 2022 - One of the steps to get the best results from injection molding requires the operator to properly set up the clamping sequence. Without an intuitive and visual experience, setting this up can be a time-consuming and d...
Read moreWant to know more about our machines?
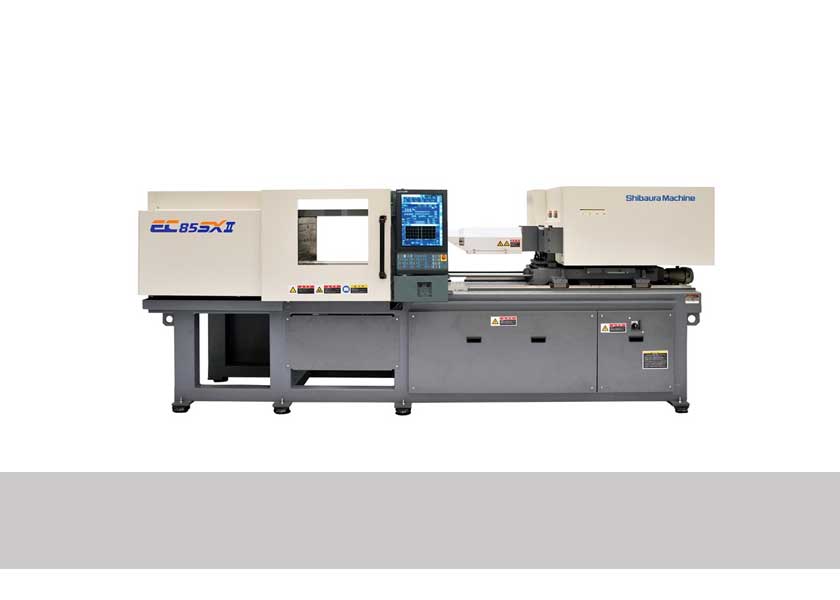
Injection Molding Machines
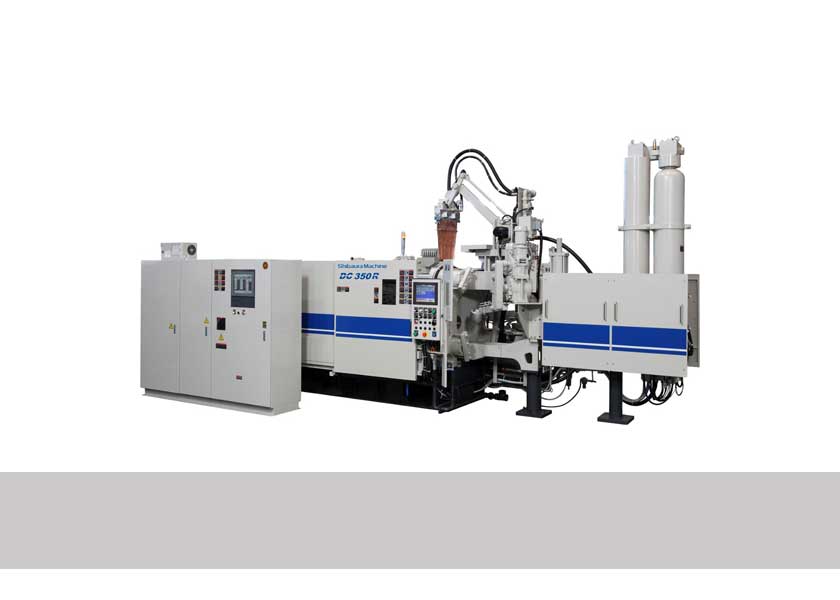
Die Casting Machines
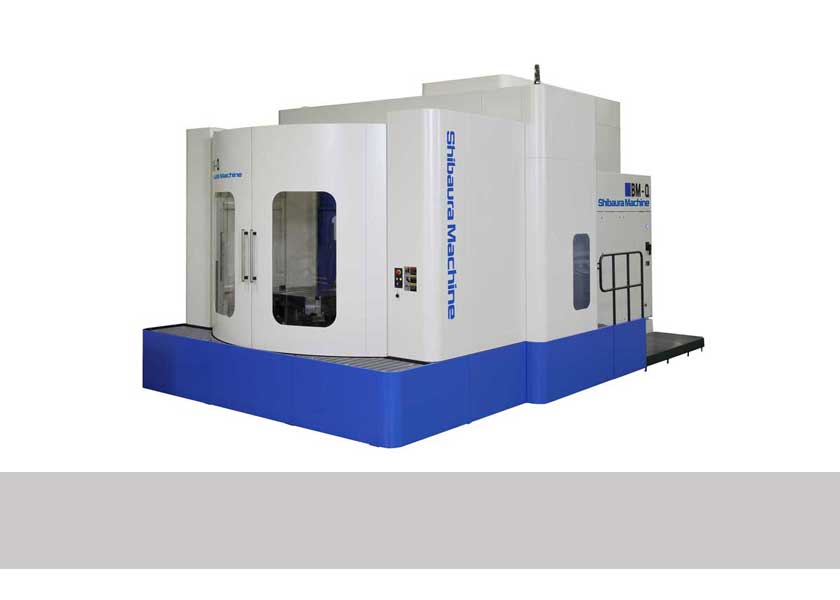
Machine Tools
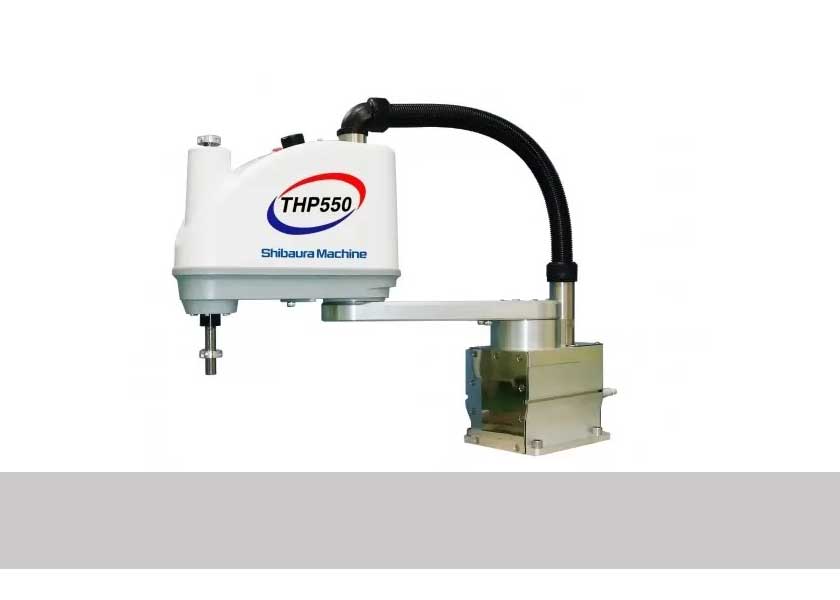