Belt Drive or Direct Drive? Shibaura Machine is Breaking Down the Differences
ELK GROVE VILLAGE, IL, September 22, 2021 - Linear motion control systems, such as direct drive and belt drive, are key in today’s motion-driven automation environment. And while both options look similar, they are fundamentally different. You will want to understand the distinct characteristics of both in order to best choose an option for your specific application.
The biggest difference between direct drive and belt drive is that a ball screw uses ball bearings to eliminate the friction between the nut and screw in the belt drive and roller screws in the direct drive do not. Because the ball screw contains a nut allowing the ball bearings to circulate it offers additional support on the load and reduced friction. What does this mean for your machine?
Consider the Design
The design of linear motion devices is essential to keep up the demand for greater reliability, lower power consumption, and higher levels of precision. For example, direct drive tends to be a common option for high-duty applications, but when efficiency and improved downtime are important, belt drive is a preferred choice. Moreover, as we see an increased push for modern injection molding machines to deliver greater power efficiency, this continues to pose a challenge for direct drive which generally requires more torque and cooling.
Shibaura Machine designed the belt drive in the all-electric SXIII series to ensure its precision and longevity. The ball retainers within the belt drive are designed to reduce wear and increase runs of the balls transfer load over a larger area, which allows retainers to assist in holding lubrication, improve durability, and reduce cooling. Because of less friction between the balls, there is reduced noise levels.
Superior Mechanical Efficiency
While the direct drive continues to remain a popular choice for manufacturers, more are now looking to machines with belt drives to improve efficiency and longevity. Generally, belt drives will be a preferred option for applications requiring high throughput, precision, speed, and reduced operational costs.
If you would like more information on Shibaura Machine’s belt drive design, contact us today.
Contact us today to see if our SXIII series can help your molding shop achieve its goals!
Related Articles View All Articles
Optimize Part Weight Consistency with the Shibaura Machine Plastrol Function
ELK GROVE VILLAGE, IL, September 2, 2021 - Part weight variations due to inconsistent check ring response can cause unwanted fluctuations and endanger a stable injection molding process. When we look for ways to stabilize the process and improve shot-to-sh...
Read moreShibaura Machine’s New Smart Factory Highlights IoT Solutions Paired With All-Electric Injection Molding Technology
ELK GROVE VILLAGE, IL, August 27, 2021 - Shibaura Machine will be launching its new Smart Factory with an open house at their Elk Grove Village, Illinois tech center in the Fall, 2021. This manufacturing cell will further support customers to fully leverag...
Read moreTaking LSR Molding to a Higher Level with All-Electric Technology
ELK GROVE VILLAGE, IL, August 20, 2021 -Liquid silicone rubber molding is experiencing demand growth like never before in North America. While many manufacturers are considering whether to invest in a dedicated liquid silicone rubber (LSR) molding machine...
Read moreTwo-Shot Molding: Any Machine, Any Time with Shibaura Machine
ELK GROVE VILLAGE, IL, August 6, 2021 - Two-shot molding is one of the most efficient processes for manufacturers creating products using plastics. By allowing operators to create multi-material or multi-colored parts without adding extra assembly steps it...
Read moreInjection Molding Energy Consumption At a Glance
ELK GROVE VILLAGE, IL, July 28, 2021 - From energy hogs forty years ago to the efficient all-electric options of today, injection molding machines have made quite the evolution. While injection molding is still an energy intensive process, the all-electric...
Read moreFrom One Product to the Next- Improving Set-up Efficiency in Injection Molding with SMED and the SXIII
ELK GROVE VILLAGE, IL, July 7, 2021 - Reducing the changeover time for your operations is critical to maintain a competitive advantage and improve profitability in the manufacturing industry today.That’s where the concept of single-minute exchange of die, ...
Read moreWant to know more about our machines?
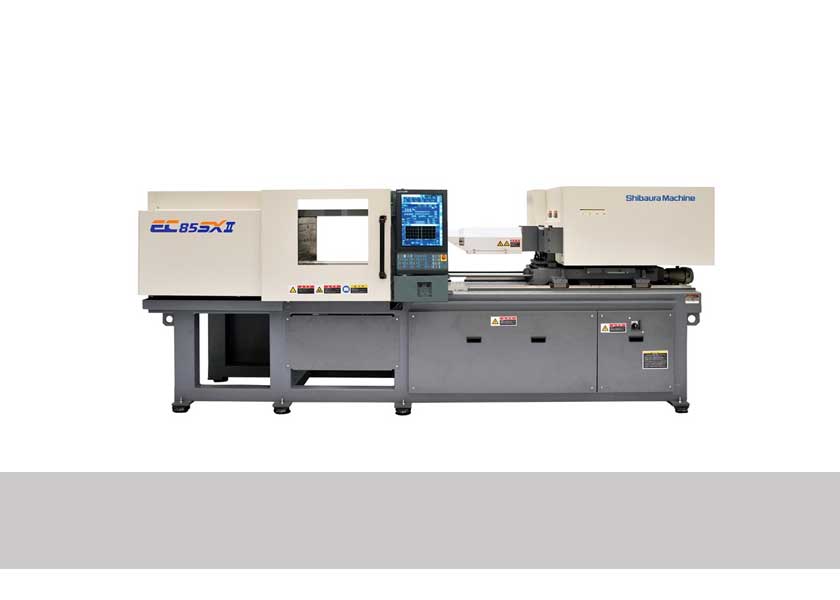
Injection Molding Machines
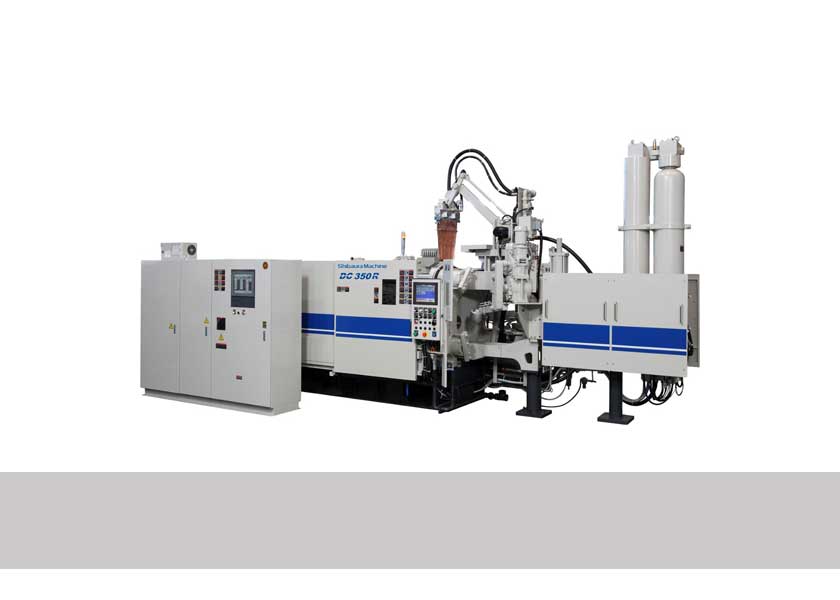
Die Casting Machines
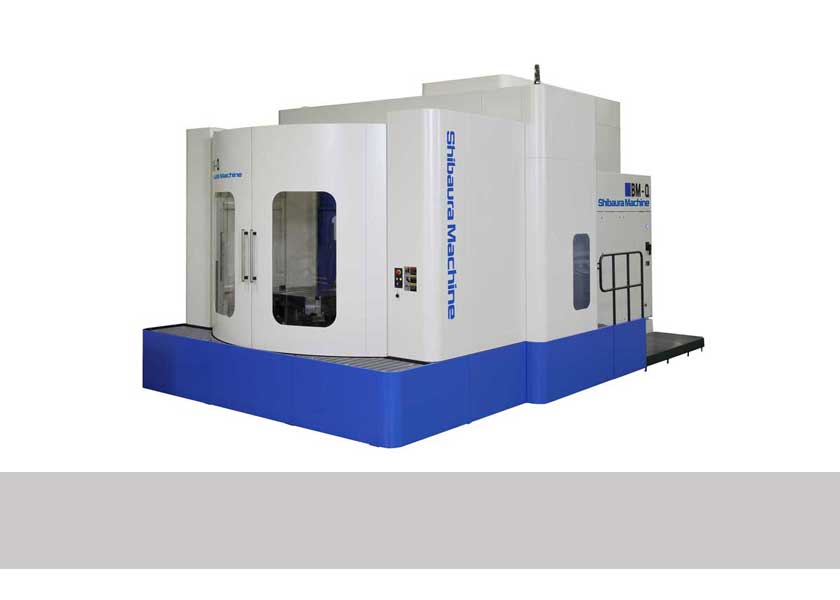
Machine Tools
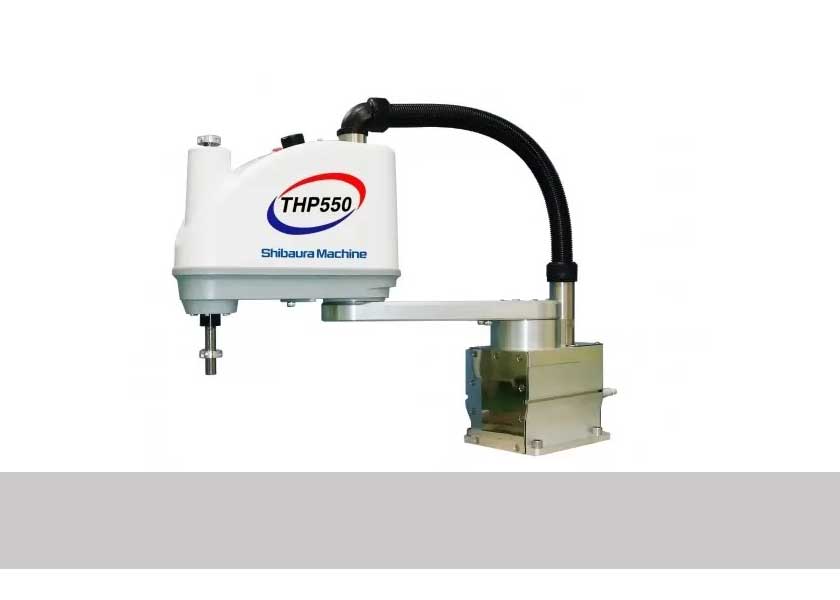