Reducing Unplanned Downtime: Harnessing the Power of machiNetCloud
ELK GROVE VILLAGE, IL, July 6, 2023 -
From lost productivity to missed deadlines and increased costs, managing downtime has become a crucial strategy for maintaining a competitive edge in today's fast-paced industry, where just-in-time production is paramount. For example, if an automated assembly line experiences downtime due to a machine malfunction, the entire production line is likely to stop until the machine can be serviced, resulting in a significant loss of productivity and revenue. This is just one example of the challenges manufacturers face due to unplanned downtime.
How Is Unplanned Downtime Affecting Your Factory?
The consequences of unplanned downtime can be far-reaching for manufacturers. Production schedules are disrupted, workflow efficiency is hampered, and costs are increased as a result. From idle workers and wasted materials to missed delivery deadlines and dissatisfied customers, the financial implications can be significant. For instance, if a critical component fails in a production line, the entire line must be shut down until the issue is resolved, resulting in lost output, labor costs, and potential customer delays. In order for manufacturers to manage these challenges, they need reliable tools that provide real-time insights and enable proactive decision-making.
Many Downtime Strategies Bring Limitations
Traditionally, manufacturers relied on reactive approaches to address downtime that often fall short of accurately tracking and addressing events. Strategies such as run-to-failure, spare parts supply, and redundancy bring their own set of challenges and limitations. To find a more efficient and cost-effective approach to reducing downtime, manufacturers have turned to process control techniques like Six Sigma.
Applied specifically to downtime tracking, Six Sigma allows operators to gain a factual understanding of downtime occurrences, their root causes, and consequences. It highlights previously unknown reasons for downtime and helps implement effective preventative maintenance strategies based on factual data about associated costs.
However, many manufacturers still rely on operators manually documenting downtime events, which is time-consuming, prone to errors, and lacks comprehensive analysis and insights. The manual process adds strain to already stretched resources and can lead to misinterpretation of data. In an era where automation and digitalization are prevalent, it is inconceivable to continue relying on manual data collection for downtime tracking.
To overcome these limitations, manufacturers require a more advanced approach. That's where machiNetCloud comes into play—a comprehensive platform that enables manufacturers to adopt Industrial IoT (IIoT) with a vertically integrated, scalable, and secure approach. By leveraging machiNetCloud, manufacturers gain access to a range of tools designed to enhance OEE, empowering them to review, evaluate, and make data-driven decisions for continuous improvement.
Proactively Improving Unplanned Downtime for Manufacturers
The machiNetCloud Downtime App offers a comprehensive solution for tracking and analyzing downtime events, providing manufacturers with actionable data to minimize unplanned downtime.
Real-Time Downtime Monitoring
The app's user-friendly interface allows operators to visualize machine downtime as it happens. By capturing and verifying downtime reasons in real-time, manufacturers can quickly identify disruption root causes. Operators can add additional information and comments, facilitating accurate analysis and enabling a proactive approach to resolving issues promptly. For instance, if a machine stops due to a broken belt, the operator can add a note ensuring the issue is documented and can be quickly addressed.
Automatic Analysis and Pareto Charts
The app's automatic analysis capabilities help separate the critical downtime events from less impactful ones. Through Pareto charts, manufacturers can prioritize their efforts and focus on the most significant downtime reasons. For example, a maintenance manager can use the data to identify which production line or machine is generating more downtime and focus their efforts on that area to reduce losses. This data-driven approach empowers operators and management to make informed decisions and allocate resources effectively to address the root causes of downtime.
Mean Time Between Failure (MTBF) and Mean Time To Repair (MTTR) Reports
By generating MTBF and MTTR reports, the machiNetCloud Downtime App provides valuable insights into equipment reliability and repair efficiency. Manufacturers can analyze how often specific error codes occur and the time required for repairs. For instance, by monitoring the MTBF and MTTR reports, the manufacturer can identify problems with specific parts and schedule necessary preventative maintenance. This information helps identify recurring issues, optimize maintenance schedules, and improve overall equipment effectiveness (OEE).
User-Configurable Automatic Alerting
The app offers user-configurable alerts through SMS, email, or push notifications. Custom alerts can be set up to notify operators and maintenance teams immediately when critical events occur. For example, an alert can be configured to notify an operator if the temperature in a certain area breaches a set threshold. Timely alerts enable swift responses, minimizing downtime incidents.
Expandability and Integration
machiNetCloud Downtime App can be expanded and integrated seamlessly with other systems and applications. For instance, it can be integrated with a customer's existing ticketing system to provide a consolidated view of all service requests and incidents. Its range of RESTful API choices allows for data integration, custom-built apps, and dashboards. Manufacturers can leverage these capabilities to create informative shop floor displays and gain comprehensive visibility into production performance.
Ready to Tackle Unplanned Downtime in Manufacturing?
Devising a reliable strategy for managing downtime is essential to ensure manufacturers remain competitive and productive. The Industrial Internet of Things (IIoT) introduces a way for manufacturers to better manage and mitigate downtime.
By using machiNetCloud's suite of applications and, in particular, the Downtime App, manufacturers can eliminate inefficiencies associated with manual downtime tracking methods. By embracing automation and digitalization, manufacturers now have the opportunity to shift from reactive to proactive downtime management, enabling them to achieve higher OEE, and drive continuous improvement in the ever-evolving manufacturing landscape.
Contact the Digital Services Division to learn more.
Related Articles View All
Building a Virtual Fortress Around Your Factory: machiNetCloud's Zero Trust Security and Amphion Devices
ELK GROVE VILLAGE, IL, June 22, 2023 - In today's manufacturing landscape, remote access to machines and automation systems has become essential for efficient operations. However, traditional perimeter security measures are no longer sufficient to protect ...
Read moreUnlocking Efficiency and Security: Best Practices for Remote Troubleshooting in IIoT-enabled Manufacturing
ELK GROVE VILLAGE, IL, May 26, 2023 - In today's rapidly evolving manufacturing landscape, remote troubleshooting and security have become critical aspects of operational efficiency and resilience. Manufacturers face the challenge of resolving issues promp...
Read moreBring Quality Management to New Levels with Digital Six Sigma
ELK GROVE VILLAGE, IL, August 17, 2022 - A streamlined quality management process not only boosts overall factory effectiveness but as a key metric to improving overall equipment efficiency (OEE), is extremely important to maintaining a competitive advanta...
Read moreHow to Bring Digital Six Sigma Process to Your Factory to Reduce Downtime
ELK GROVE VILLAGE, IL, July 28, 2022 - What strategies has your factory taken on to reduce the amount of unplanned downtime due to machine issues? From preventative maintenance to redundancy, and even increasing planned downtime to reduce unplanned downtim...
Read moreHow IIoT is Improving Six Sigma
ELK GROVE VILLAGE, IL, July 15, 2022 - Over the years, Six Sigma practices have created billions of savings for the manufacturing world. Working towards the fundamental goal of creating the most efficient system possible and eliminating waste, Six Sigma pr...
Read moreA Better Way to Track Downtime in Manufacturing is Finally Here
ELK GROVE VILLAGE, IL, May 18, 2022 - Avoiding unplanned downtime and minimizing planned downtime is the golden ticket to manufacturing success. Through the years, manufacturers have implemented various strategies to maximize machine utilization and suppor...
Read moreRemote Troubleshooting is Less Complex Than You Think
ELK GROVE VILLAGE, IL, April 29, 2022 - Industrial machinery is the lifeblood of manufacturers. As many begin to recover and restart in the next normal, many see it as an opportunity to reimagine a future with increased digitization to create more resilien...
Read moreCreate a True Path Forward to Improving Your OEE with machiNetCloud
ELK GROVE VILLAGE, IL, April 14, 2022 - When it comes to operation optimization many manufacturers are still left wondering the best ways to move forward. Utilizing spreadsheet and clipboard methods are still commonplace, but unfortunately lacks the detail...
Read moreWant to know more about our machines?
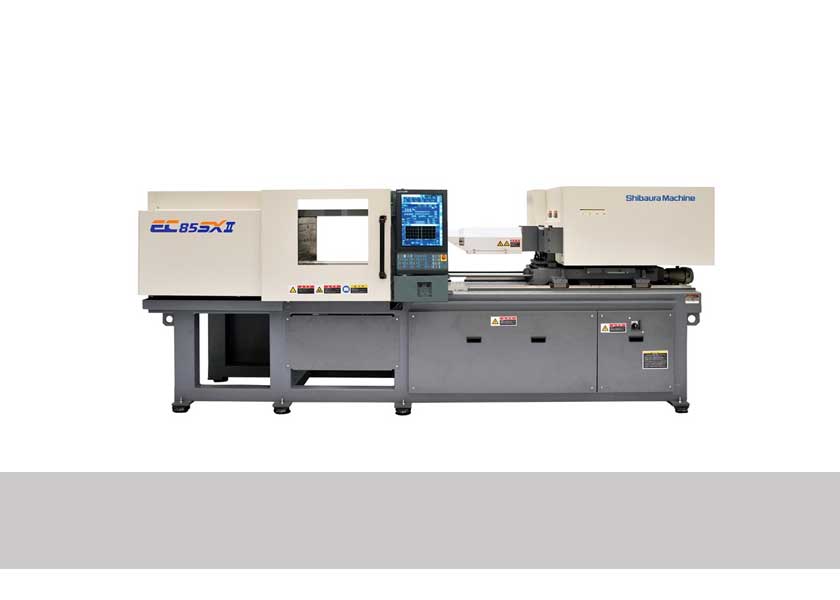
Injection Molding Machines
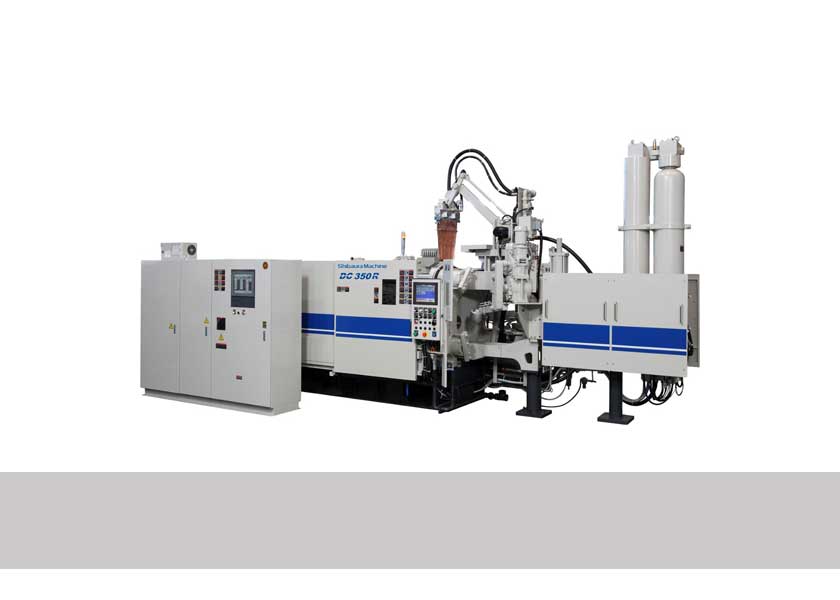
Die Casting Machines
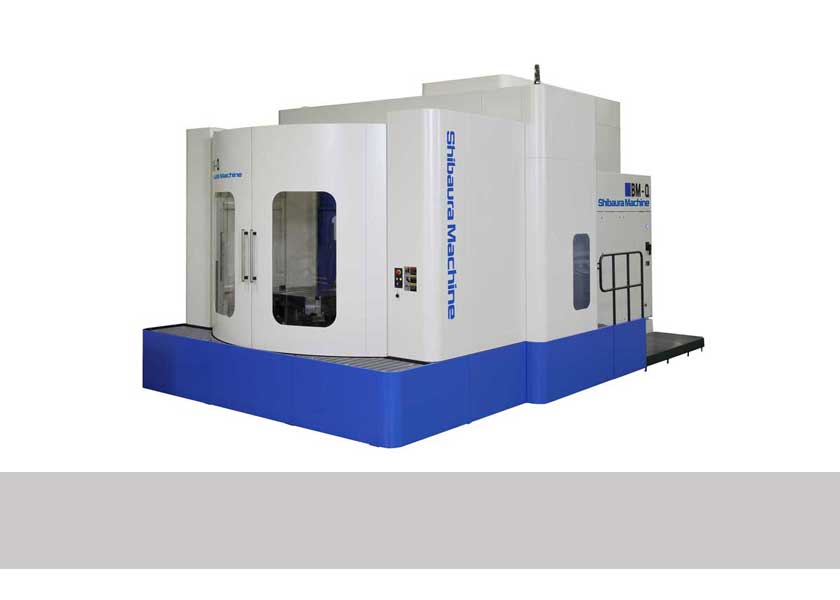
Machine Tools
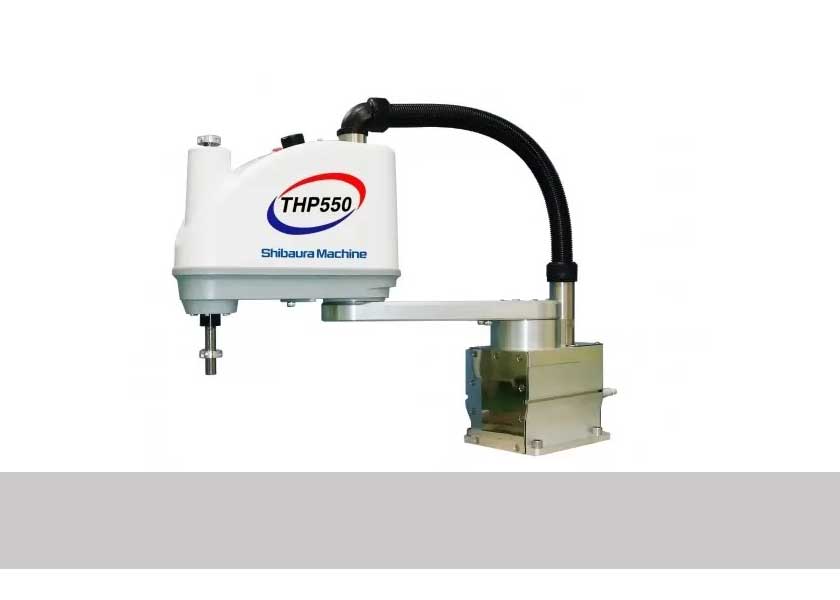