Improving Production Through Digital Six Sigma and Recipe Management
ELK GROVE VILLAGE, IL, November 10, 2022 -
In order to improve productivity and work towards a higher Overall Equipment Efficiency (OEE), many manufacturers in injection molding and die casting industries have turned to recipe management as an essential tool in creating quality products efficiently. Recipe management also aligns perfectly with Six Sigma processes, allowing for quicker continuous improvement with the DMAIC cycle (Define, Measure, Analyze, Improve and Control) by validating and monitoring the integrity of production setpoints.
Continuously Improving Production
Shifting from Six Sigma to Digital Six Sigma enlists the help of technology, namely the Industrial Internet of Things (IIoT). Shibaura Machine’s machiNetCloud IIoT solution applies recipe management and, makes adopting Digital Six Sigma processes easy by ensuring machine setpoints are optimized. Ultimately, it leads to more dependable production with higher quality, reduced changeover times, and fewer operator errors.
Machines connected to the machiNetCloud platform collect and record all aspects of the machine’s operational datapoints that are important to production quality. These data points include machine setpoints and actual quality data points for all production jobs. By grouping the machine setpoints into “recipes” and, checking the actual values against dynamic limits, machiNetCloud's Recipe management app with the aid of Artificial Intelligence (AI) provides sophisticated learning algorithms that define the best recipes (“Golden Run”).
With a one-click, you can store recipes, continue to monitor their efficiency and configure alarms to alert you of excessive machine setpoint variations. Correlating recipe data with the OEE of the machine, organizations can push “Golden” recipes to the entire factory or, to multiple sites. This means continuous improvements in speed, efficiency, and manufacturing quality.
Learn More
Using Digital Six Sigma and the Recipe Management app give you better control over your manufacturing process and achieves better performance. Contact the Digital Services Division to learn more.
Related Articles View All
Bring Quality Management to New Levels with Digital Six Sigma
ELK GROVE VILLAGE, IL, August 17, 2022 - A streamlined quality management process not only boosts overall factory effectiveness but as a key metric to improving overall equipment efficiency (OEE), is extremely important to maintaining a competitive advanta...
Read moreHow to Bring Digital Six Sigma Process to Your Factory to Reduce Downtime
ELK GROVE VILLAGE, IL, July 28, 2022 - What strategies has your factory taken on to reduce the amount of unplanned downtime due to machine issues? From preventative maintenance to redundancy, and even increasing planned downtime to reduce unplanned downtim...
Read moreHow IIoT is Improving Six Sigma
ELK GROVE VILLAGE, IL, July 15, 2022 - Over the years, Six Sigma practices have created billions of savings for the manufacturing world. Working towards the fundamental goal of creating the most efficient system possible and eliminating waste, Six Sigma pr...
Read moreA Better Way to Track Downtime in Manufacturing is Finally Here
ELK GROVE VILLAGE, IL, May 18, 2022 - Avoiding unplanned downtime and minimizing planned downtime is the golden ticket to manufacturing success. Through the years, manufacturers have implemented various strategies to maximize machine utilization and suppor...
Read moreRemote Troubleshooting is Less Complex Than You Think
ELK GROVE VILLAGE, IL, April 29, 2022 - Industrial machinery is the lifeblood of manufacturers. As many begin to recover and restart in the next normal, many see it as an opportunity to reimagine a future with increased digitization to create more resilien...
Read moreCreate a True Path Forward to Improving Your OEE with machiNetCloud
ELK GROVE VILLAGE, IL, April 14, 2022 - When it comes to operation optimization many manufacturers are still left wondering the best ways to move forward. Utilizing spreadsheet and clipboard methods are still commonplace, but unfortunately lacks the detail...
Read moreWant to know more about our machines?
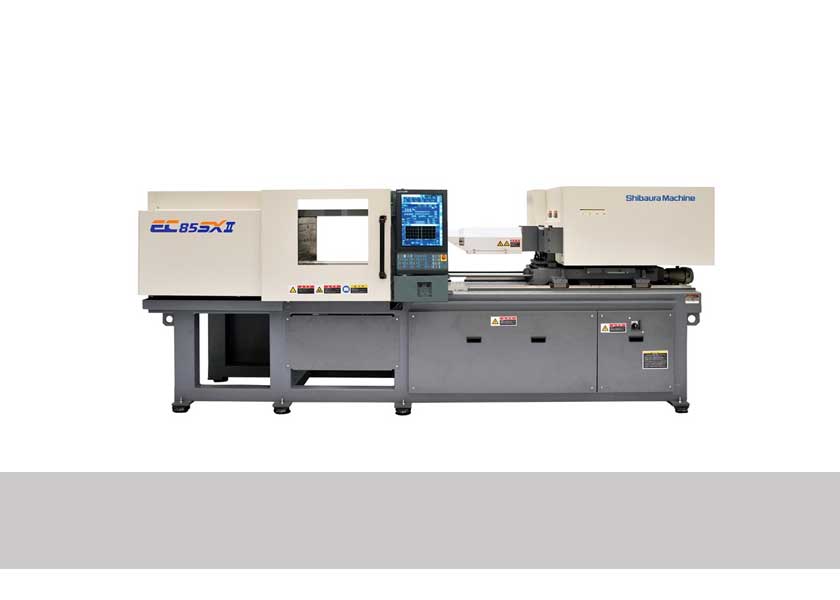
Injection Molding Machines
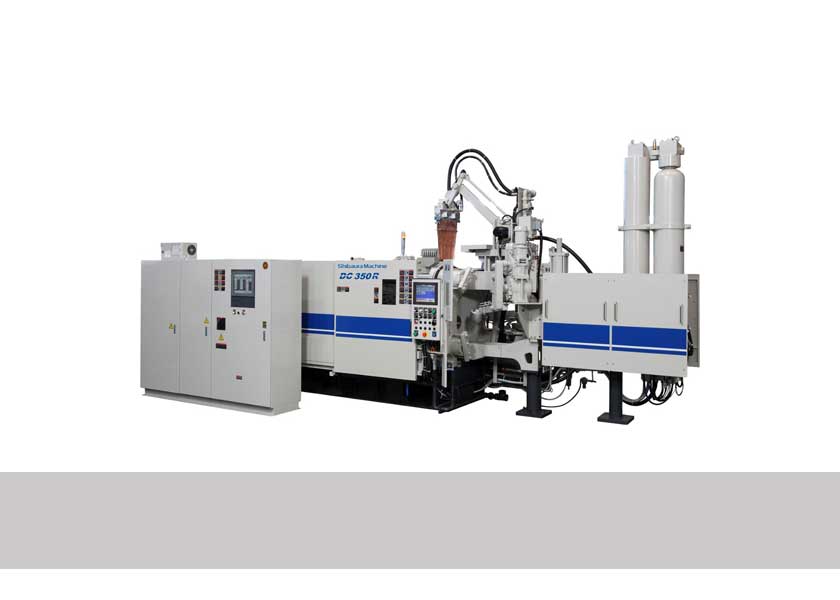
Die Casting Machines
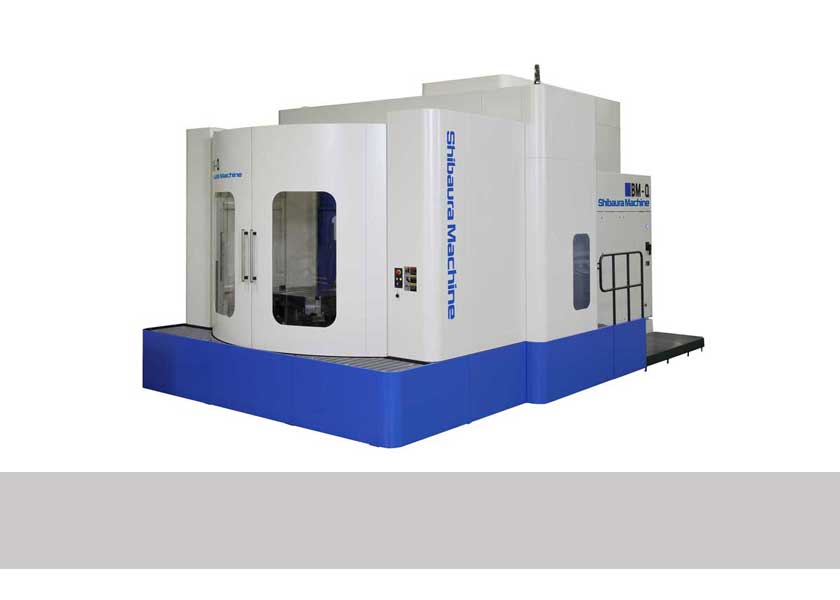
Machine Tools
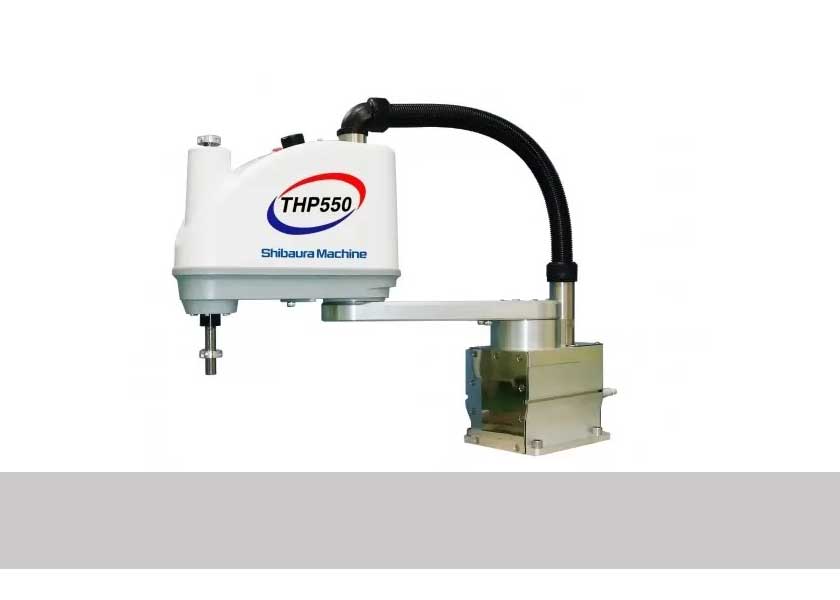