Start Improving Production With the Help of a Quick Change Workholding
ELK GROVE VILLAGE, IL, March 22, 2023 -
In the world of manufacturing, time is money. Any downtime or delay in the production process can have a significant impact on a company's bottom line.
This is where quick change workholding comes into play. Also known as quick change fixturing, this technology is a type of workholding system used in machining operations that allows operators to quickly and easily change out parts or workpieces without the need for time-consuming and costly setup changes.
The quick-change workholding system leverages the unique capabilities of machine tools, such as their remarkable precision and high speeds/forces, and enables manufacturers to switch out fixtures quickly and easily, which leads to several benefits for their production processes.
Streamlining Manufacturing Processes
When it comes to maximizing spindle usage, quick change workholding systems have proven to be a highly effective method for enhancing productivity. In the case of vertical turning lathes (VTLs), such as Shibaura Machine’s Model TUE-200(S), and horizontal boring mills (HBMs) like Shibaura Machine Model BTH-130.R24, this can be particularly beneficial because typical workpieces for these machines are generally more complex with larger dimensions and heavier weights.
Changing out parts or workpieces typically involves removing the fixture and all associated components, and then re-setting everything up for the new part. Quick change workholding, on the other hand, streamlines this process by using modular components that can be easily swapped out as needed. This technology typically involves the use of a quick change fixture plate system with a ball lock mechanism for locating and locking fixtures onto machine tables and subplates quickly and accurately.
Several benefits manufactures recognize with the use of quick change workholding systems include:
Increased productivity
Change out fixtures in mere minutes rather than hours, which means less downtime and more time spent on actual machining.
Greater flexibility
Different parts and fixtures can be easily swapped in and out. This makes it easier to handle smaller production runs or make changes on the fly.
Improved accuracy
Because the fixture's location is already known within the machine, there is less chance for human error in setting up the workholding, allowing for improved accuracy and consistency in machining.
Reduced setup time
The need for time-consuming and labor-intensive setup procedures is eliminated, which can significantly reduce overall setup time. This means that machines can be up and running faster, which is especially beneficial for shorter production runs.
Increased safety
These systems often incorporate safety features such as interlocking mechanisms, which can prevent accidents and injuries caused by incorrect setup or operation.
All of these benefits can translate into significant cost savings over time. This is especially true for high-volume production runs, where even small improvements in efficiency can have a big impact on the bottom line.
Customized for Your Shop’s Needs
There are several types of quick-change workholding systems available for VTLs and HBMs. The choice of system will depend on factors such as the size and weight of the workpiece, the accuracy and repeatability required, and the specific requirements of the machining operation.
Contact the Machine Tool team to learn more about developing a customized production solution for your Shibaura Machine VTL Model TUE-200(S) and HBM Model BTH-130.R24.
Related Articles View All Machine Tools Articles
Maximizing Efficiency in Machining with the Right Angle Head Attachment on your Horizontal Boring Machine
ELK GROVE VILLAGE, IL, March 14, 2023 - As a machine tool operator, you know that there are many challenges involved in performing precision cutting, drilling, and other operations. Machining complex workpieces with multiple surfaces often require numerous...
Read moreBoost Your CNC Machining Confidence: On-Site Training Explained
ELK GROVE VILLAGE, IL, March 7, 2023 - As the manufacturing industry continues to grow and evolve, it's becoming increasingly important for companies to invest in their workforce through proper training programs.In the world of machine tools, on-site train...
Read moreMachine Tool Automation Options for Shibaura Machine's TMD Series
ELK GROVE VILLAGE, IL, February 28, 2023 - Efficiency and productivity are critical factors for success in today's fast-paced manufacturing industry. To maintain a competitive edge, manufacturers must continually seek new ways to optimize their processes a...
Read moreCritical Factors to Consider With Your Machine Tool Foundation
ELK GROVE VILLAGE, IL, February 15, 2023 - Machine tools are the backbone of the modern manufacturing industry and play a critical role in the production of goods and services. While the machine tools themselves are the main focus, their foundation is a cr...
Read morePolar Coordinate Interpolation: Unlocking New Possibilities with Shibaura Machine Tools
ELK GROVE VILLAGE, IL, February 7, 2023 - Have you ever felt like your machining operations were stuck in a straight line? Polar Coordinate Interpolation may be the answer you've been searching for. With this motion control method, you can upgrade your mac...
Read moreMaking Sense of Machine Tool Thread Milling for Your Application
ELK GROVE VILLAGE, IL, January 30, 2023 - When it comes to adding threads to a workpiece, the choice of method can make a significant difference to the outcome. For parts made from difficult-to-machine materials, thread mills have become an increasingly po...
Read moreWant to know more about our machines?
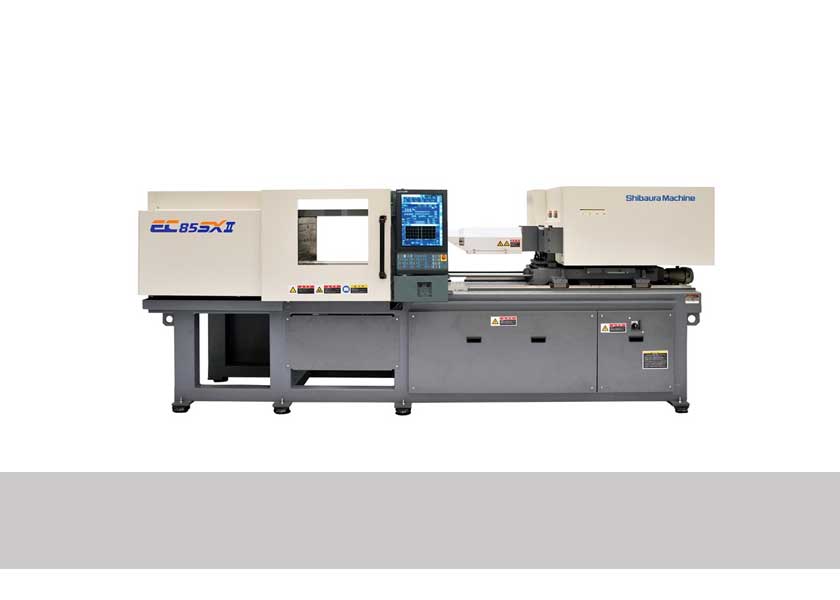
Injection Molding Machines
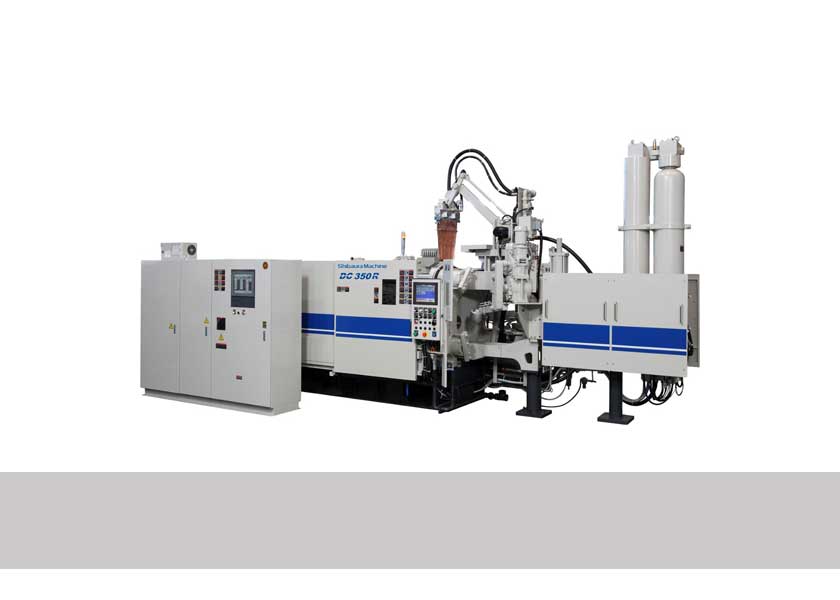
Die Casting Machines
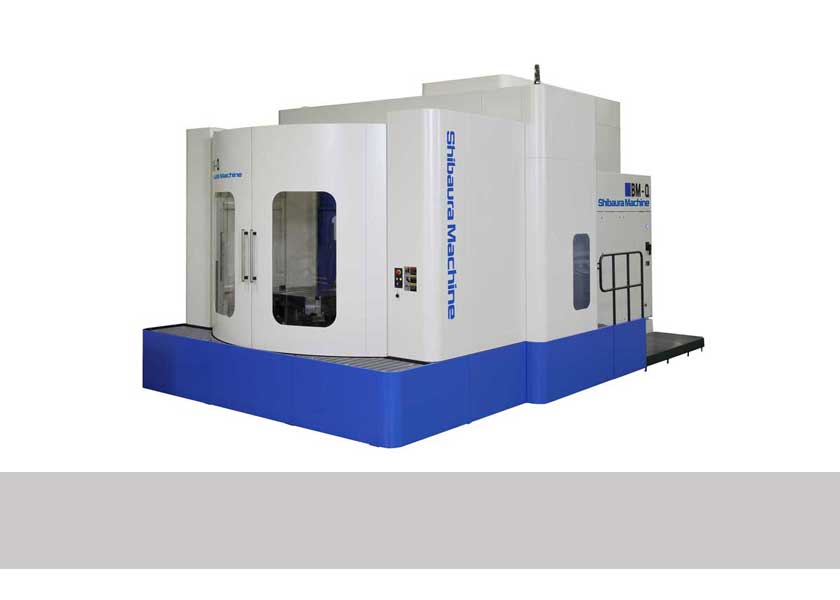
Machine Tools
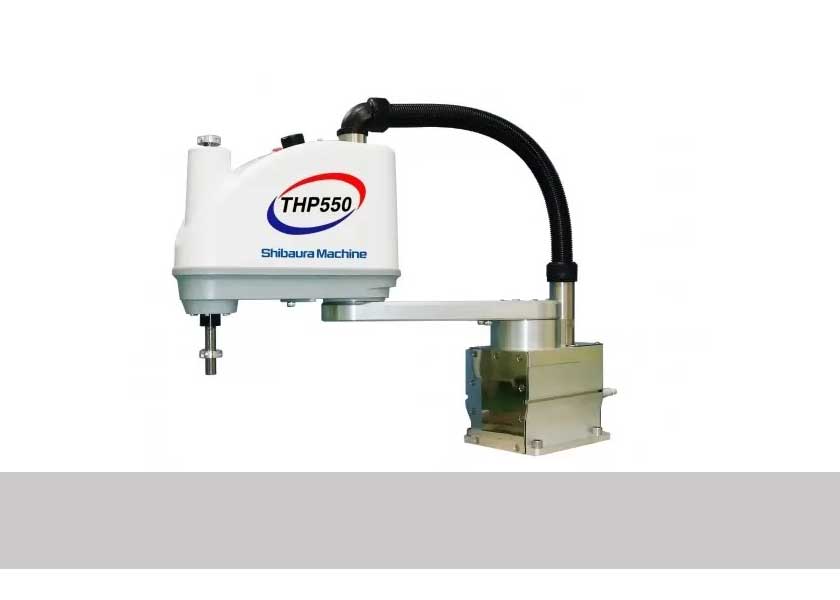