Advancing Sustainability & Efficiency in Die Casting
ELK GROVE VILLAGE, IL, February 12, 2025 -
Efficiency has always been a cornerstone of manufacturing innovation. Over two centuries ago, James Watt revolutionized power generation with his steam engine. At the time, coal mines relied on horses to lift water from flooded shafts, and Watt needed a way to demonstrate how his invention could outperform them. He introduced the concept of horsepower—a unit measuring how much work his engine could accomplish compared to a horse, lifting 550 pounds one foot in one second.
Watt’s analogy was brilliant in its simplicity: saving horsepower meant reducing unnecessary work. Today, the same principle drives innovation in modern hydraulic systems. Hydraulic horsepower depends on flow rate and pressure, making it clear that reducing flow when demand is low is one of the simplest ways to save energy and increase efficiency.
Hydraulic Power: A Key to Modern Manufacturing Savings
At the core of hydraulic systems lies the relationship between power, flow rate, and pressure. Traditionally, hydraulic pumps run at a constant speed, moving a fixed volume of fluid—even when no work is required. This creates inefficiencies like wasted energy, excess heat, and wear on components. The lesson from Watt’s analogy still applies: when there’s no work to do, don’t over run the pump.
The solution lies in smarter power management. Variable pump speed technology adjusts the pump’s speed to match real-time needs, eliminating inefficiencies. This approach allows manufacturers to conserve energy, reduce heat, extend component life, and ensure optimal performance—all while meeting the demands of modern manufacturing.
The Variable Speed Motor Drive Solution
Variable speed motor drive technology adjusts hydraulic pumps to adjust their speed based on real-time requirements. When less hydraulic volume is needed, the motor slows down, conserving energy. When demand increases, the motor speeds up, optimizing flow and pressure. This dynamic system minimizes energy consumption, reduces heat generation, and decreases the need for extensive cooling—delivering a crucial efficiency upgrade for modern manufacturing.
Advantages of Variable Pump Speed Technology
Cost Savings and ROI: Variable pump speed technology offers significant energy savings compared to constant-speed motors, reducing machine operational energy consumption by approximately 40%. This directly lowers the machine operational costs, with a measurable return on investment (ROI) achieved in a short timeframe. Additionally, the reduced heat generation minimizes cooling requirements, further cutting costs associated with energy and maintenance.
Increased Productivity: By adapting to real-time hydraulic fluid demands, variable speed motor drive technology enhances hydraulic performance. This ensures consistent output, fewer interruptions from overheating or wear-related downtime, and smoother transitions during high-pressure operations—leading to more reliable production cycles and improved overall efficiency.
Reduced Maintenance Costs: Traditional hydraulic systems often have excessive wear due to constant-speed operations that exceed demand. Variable pump speed technology reduces unnecessary rotations, minimizing wear on key components like pump vanes, seals, and valves. With less unforeseen downtime and simplified maintenance requirements, manufacturers save both time and money.
Beyond cost and energy efficiency, variable pump speed technology delivers a range of operational benefits:
- Extended Component Life: Fewer pump rotations and smoother pressure transitions significantly reduce wear and tear on hydraulic components, prolonging their lifespan.
- Simplified System Design: Streamlined hydraulic pressure and flow management make the system easier to maintain and more reliable in operation.
- Noise Reduction: Slower motor speeds result in quieter operation, creating a more comfortable and safer work environment.
Sustainability in Action
The adoption of variable pump speed technology has significant benefits for sustainability in the die casting industry. It reduces energy use and heat, cutting costs and lowering the carbon footprint. Longer-lasting hydraulic parts also mean less waste and fewer resources needed, helping both businesses and the environment.
Leading the Way in Variable Pump Speed Technology
For over 75 years, Shibaura Machine has stood at the forefront of innovation, blending decades of servo motor expertise with precision engineering. Our implementation of variable speed hydraulic motor technology reflects this commitment, delivering a reliable, efficient solution to reduce energy consumption and support sustainability goals.
Shibaura Machine’s advanced die casting machines feature cutting-edge technology, offering variable speed motor drive systems for hydraulic pumps and electric servo toggle clamping linkage systems. Designed with commercially available components, these systems ensure seamless integration, improved uptime, long-term reliability, and enhanced productivity—all while aligning with global efforts to reduce environmental impact.
At Shibaura Machine, we don’t just innovate—we set the standard for efficiency and sustainability in die casting. Discover the next evolution in manufacturing and join us in building a more sustainable, efficient future.
Shibaura Machine Company, America, is a premier provider of advanced manufacturing solutions. With a strong commitment to innovation, quality, and sustainability, we deliver products that not only meet but exceed customer expectations.
Learn more about Shibaura Machine Company, America and the future of die casting contact our Die Casting Team.
- Phone: 888-593-1616
- Email: dc-sales@shibaura-machine.com
Achieving manufacturing excellence has never been easier.
Want to know more about our machines?
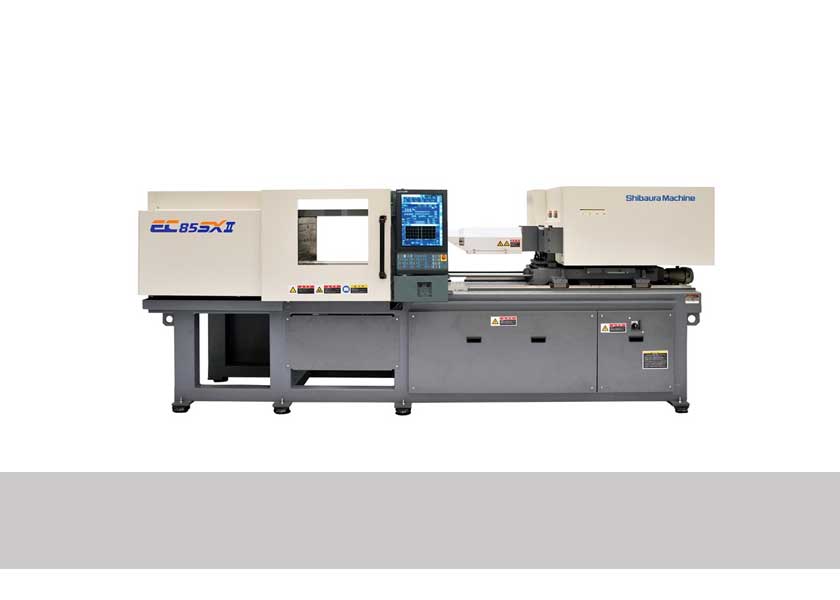
Injection Molding Machines
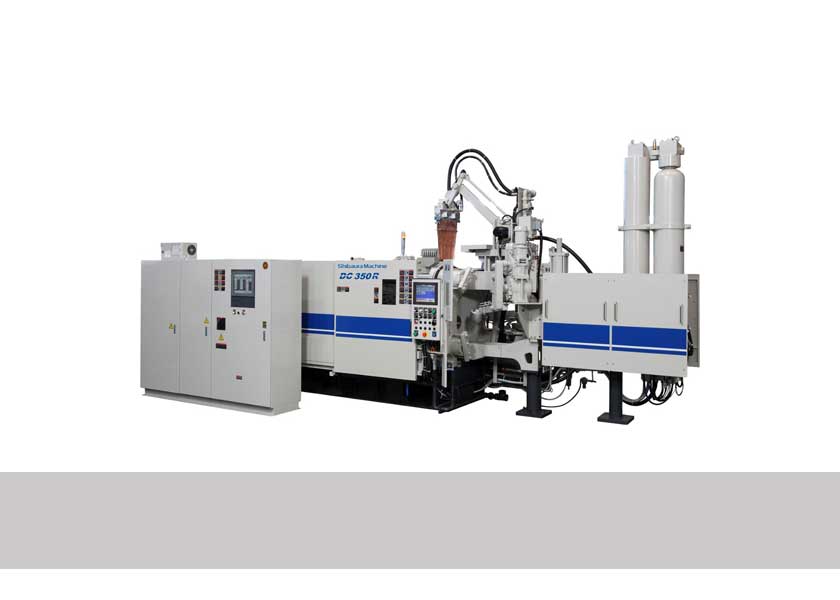
Die Casting Machines
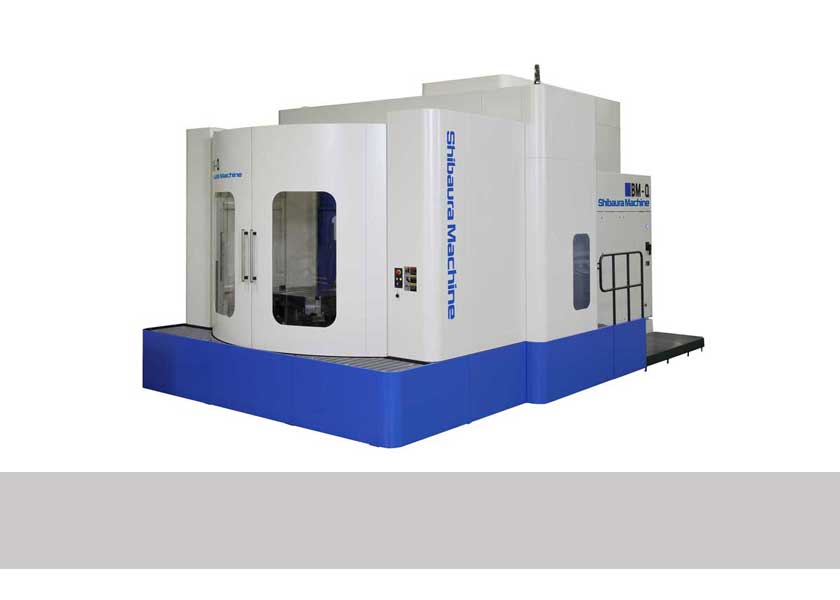
Machine Tools
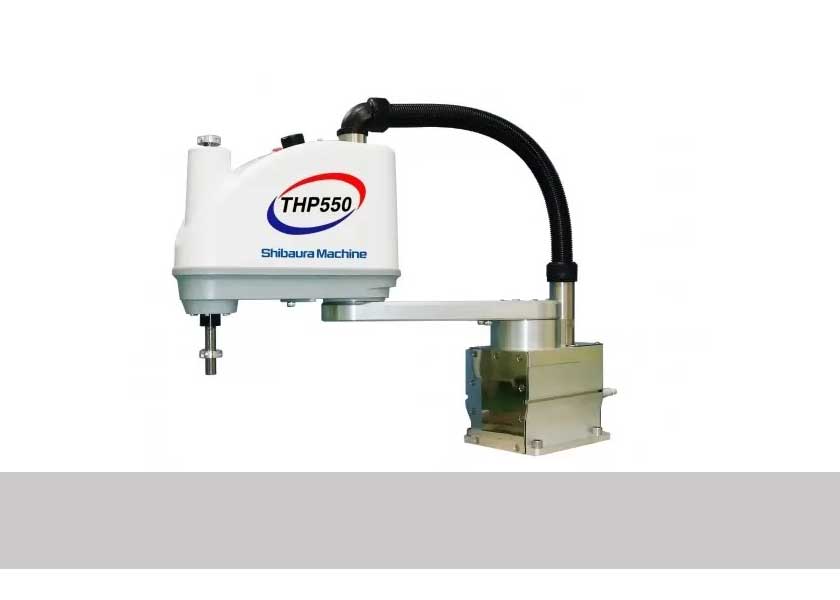