Uncovering the Hidden Economics of Die Casting: Costs and Savings
ELK GROVE VILLAGE, IL, October 17, 2024
In the die casting industry understanding the full spectrum of costs is crucial for maintaining profitability. While initial capital investments are significant and typically well-accounted for, ongoing consumable and operational costs can often be less visible but equally impactful.
What are these hidden costs and potential savings in die casting, and how can they be optimized? This article sheds light on these often-overlooked aspects to help improve efficiency and profitability.
1. Initial Capital Costs vs. Ongoing Consumables
The initial capital cost of a die casting machine and its related infrastructure is a one-time expense. This cost is usually amortized over the lifespan of the equipment and factored into the operating costs per hour or day. However, it’s the shot-to-shot costs that can significantly affect the profitability of a die casting operation.
While obvious costs like wear components (tips, cold chambers) are well-known and accounted for, smaller consumables such as plunger lubricants and die lubricants often get hidden in broader budget categories like store stock or MRO (Maintenance, Repair, and Operations). These items are replaced as needed, but their consumption per shot or casting isn’t always meticulously tracked, leading to unnoticed expenditures.
Shibaura Machine’s die casting machines are designed to optimize consumable use. The TOSCAST controller provides precise control over the casting process, ensuring that lubricants and other consumables are used efficiently. By controlling usage in real-time, the TOSCAST helps minimize consumable costs, preventing them from becoming hidden expenses.
2. Indirect Labor Costs: A Hidden Burden
One of the most overlooked costs in die casting is the indirect labor associated with producing quality castings. This includes the efforts of supervisors, process engineers, quality staff, and die repair teams who spend time addressing issues related to poorly designed or worn-out dies. Secondary labor costs are seldom tracked, but when multiple personnel focus on resolving a single problem casting, the cost can far exceed the casting’s sales price.
Shibaura Machine’s TOSCAST controller enhances process stability and quality control, reducing the frequency and severity of issues that require indirect labor. The machine is able to document process changes in real-time, allowing it to track when parameters are adjusted. This capability not only ensures consistent casting quality but also minimizes the need for interventions by supervisors and engineers. Consequently, the reduction in process-related interruptions directly helps with indirect labor costs, thereby lowering the hidden burden on production.
3. Tool Repair Costs: Hidden in Plain Sight
Repairing old dies is another cost that can easily go unnoticed, especially if the work is done internally. In contrast, sending tools out for repair incurs a visible expense. To address this, treat internal tool repair as if it were outsourced, with the production department receiving a “bill” for die repairs. This approach not only makes the costs more visible but also encourages better maintenance practices to avoid unnecessary expenses.
Shibaura Machine’s robust die casting machines are built to last, reducing the frequency of tool repairs. Additionally, the TOSCAST offers diagnostic features that can help to prevent die wear and tear. This preventative maintenance capability helps keep repair costs visible and manageable.
4. Consumable Quality and Machine Maintenance
Hydraulic fluid and other lubricants are often hidden costs because they appear as MRO items. However, using poor-quality fluids can lead to significant expenses down the line, such as damage to high-cost machine components. This is akin to “robbing Peter to pay Paul”—cutting costs in one area only to incur higher costs elsewhere.
Shibaura Machine emphasizes the use of high-quality consumables compatible with their machines. The TOSCAST ensures that only the right type and quantity of fluids are used, protecting machine components from damage. This proactive approach helps avoid hidden costs associated with poor maintenance practices.
5. Energy Consumption: A Systemic Cost
The direct power cost of operating die casting machines is a hidden yet systemic cost. Much like turning off lights when not in use, machines and auxiliary systems should be powered down when idle.
Shibaura Machine’s electric close machines and servo variable speed hydraulic drives are designed to save electrical power by using energy only when necessary, thus reducing overall power consumption.
Maximizing Cost Savings with Shibaura Machine
By closely monitoring consumable usage, implementing better maintenance practices, and leveraging advanced technologies, manufacturers can uncover and mitigate hidden costs, thereby enhancing the profitability of their die casting operations.
Shibaura Machine Company, America stands ready to assist with cutting-edge solutions that optimize both visible and hidden aspects of the die casting process and costs.
Contact our team to learn more about maximizing your investment.
If you have any questions, or require additional assistance, please contact our sales department at:
- Phone: (888) 593-1616
- Email: dc-sales@shibaura-machine.com
Achieving manufacturing excellence has never been easier.
Want to know more about our machines?
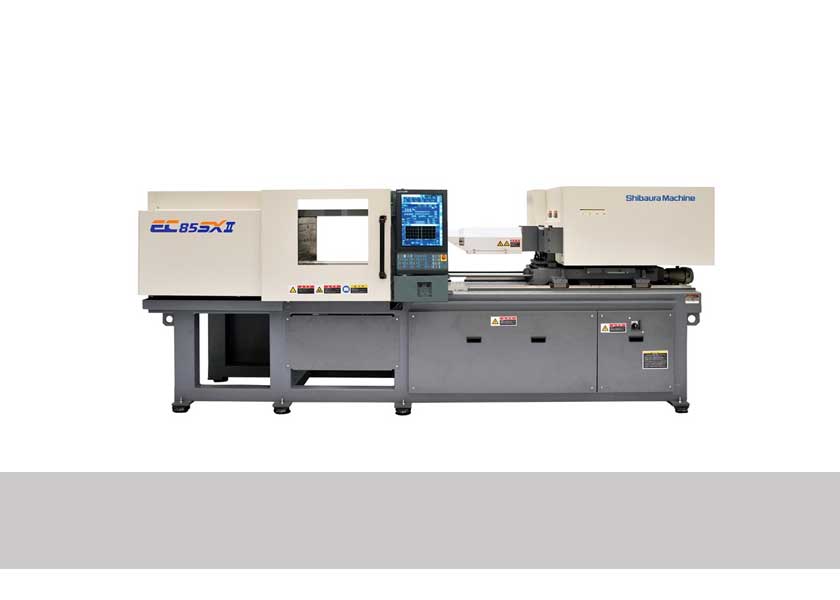
Injection Molding Machines
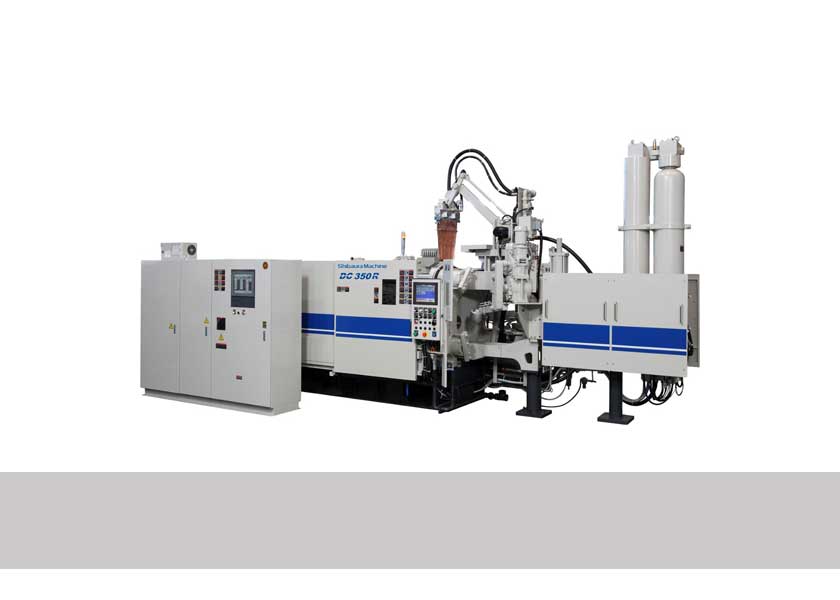
Die Casting Machines
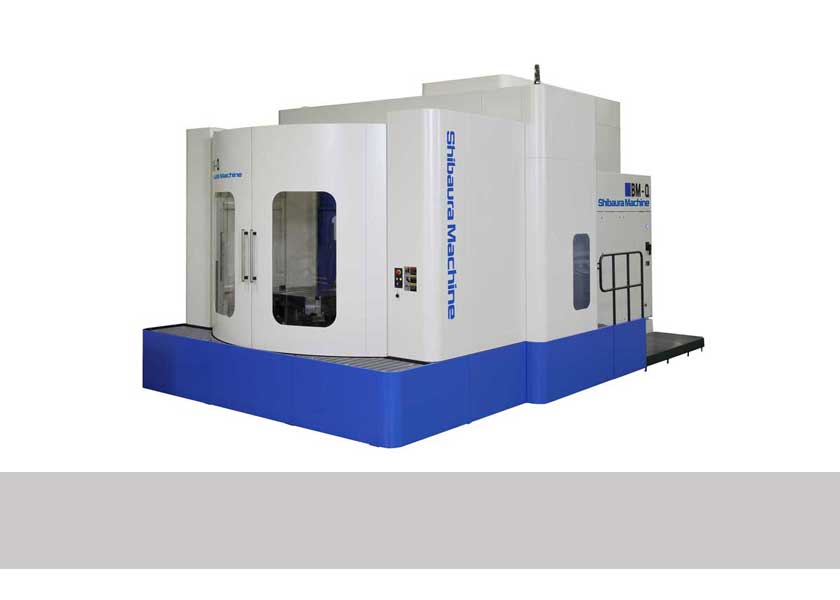
Machine Tools
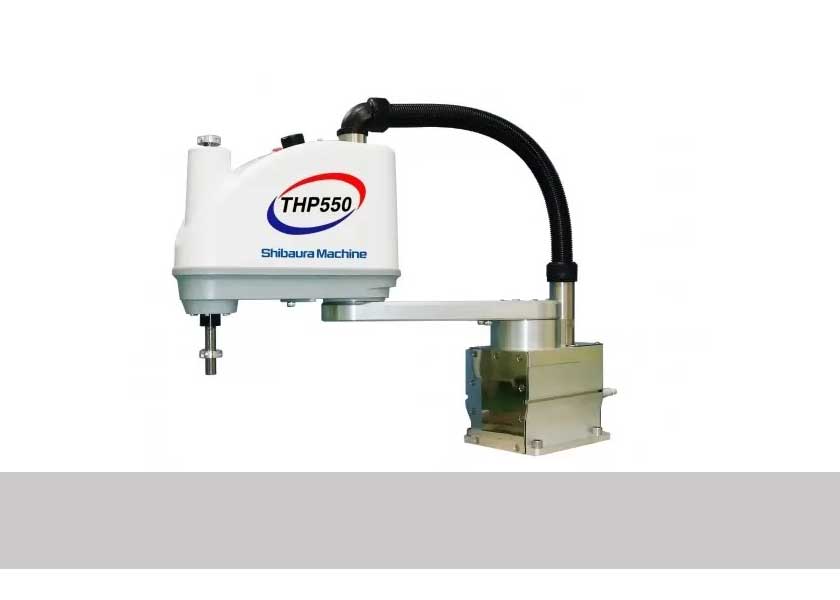